In Part 1 of our blog series on Industrial Hygiene Program Management, “SEGs: The Foundation of a Great Industrial Hygiene Program”, we learned how to create similar exposure groups (SEGs). This step of characterizing your workplace and forming SEGs is a prerequisite for performing qualitative exposure assessments (QEAs).
If you haven’t already, we recommend reviewing Part 1 on SEGs and downloading both our IH Program Cycle Infographic and IH Program Guide on the 7 steps to effective industrial hygiene (IH) program management.
What are QEAs?
Once you have established your SEGs, the next step is to assess the exposure risks to them. The industrial hygiene profession uses the term qualitative exposure assessment or QEA for performing a risk assessment for industrial hygiene concerns. It’s simply an estimation of the potential health risks for each SEG. Some of your SEGs may have sampling data to help you with quantifying exposure risk, while others will have no hard data and require you to determine their risk through other methods, including your best professional judgement!
QEAs have been done informally since the 1950’s, and were formally recognized when AIHA published their first version of, “A Strategy for Occupational Exposure Assessment” in 1991. Since then, AIHA has published several updates to the text and QEAs are now widely considered a best practice for industrial hygiene around the world.
The end product of performing QEAs is a risk rating that can be used to prioritize resources for IH sampling, implementation of controls and inclusion of workers in medical surveillance programs. QEAs can also identify high-risk potential exposures that require immediate corrective actions, rather than taking the time and effort to perform IH sampling and waiting for analytical results to be returned from the lab.
In this article, we cover several of the most common methods used to perform QEAs. Additionally, we help you begin to set up a simple risk matrix report that can be used to easily prioritize and communicate potential exposure risks for workers and management.
QEAs as Part of Your IH Program
While SEGs are the foundation of a good IH program, QEAs are the actionable insights which drive your IH program. Once performed, they provide a comprehensive and visual breakdown of the potential risks of your workplace so you can get to work protecting workers. Here are some of the greatest benefits of performing QEAs:
Simple: QEAs do not need to be complex, use complex models or require a strong knowledge of statistics. With training, QEAs can be performed by EHS staff with even limited IH expertise.
Quicker & cheaper: Sampling to quantify each potential exposure to each worker could take years and be prohibitively expensive. QEAs enable even the smallest of IH budgets to pack a punch – accurately and comprehensively assessing risks in a fraction of the time and cost.
Comprehensive: QEAs provide a tool to quickly document all potential exposures, including those with minimal exposure risks. This is commonly known as “negative exposure documentation”. This provides a more extensive risk profile compared to sampling only the higher-risk SEGs.
Prioritization: Once completed, QEAs make it easier to identify SEGs that require additional investigation and monitoring. SEGs with sufficient data and a high degree of confidence showing they do not require a significant investment in additional monitoring can be more effectively prioritized.
Improved communication: QEAs ultimately help you create a well-developed risk matrix that standardizes risk visualization across disciplines, and provides a valuable tool to show workers and management what IH offers and the benefit it brings to the company.
Litigation Support: Well-documented QEAs and other IH program information can provide faster access to supporting data without needing to recall files from storage and spend weeks going through old reports.
Knowledge Transfer: QEAs provide a great way to capture the knowledge drawn from your EHS professionals’ years of experience, and integrate that knowledge into your IH program for future IH leaders.
How do I Perform QEAs?
In Part 1 of our series, “SEGs: The Foundation of a Great Industrial Hygiene Program”, we discussed how an example population of 250 workers at the Houston Refinery were assessed and assigned to Similar Exposure Groups (SEGs).
Step #1: List any significant stressors for each SEG.
How do you identify what potential stressors should be listed? Sources for this information include:
- Walk-through surveys
- Interviews with workers and Engineers
- Chemical inventories & SDSs
- Previous sampling data collected
- Injury/illness recordkeeping logs
Once you have gathered this information, list all of the potential stressors for each SEG. An example of this is shown below in Table 1 (this should be familiar from Part 1):
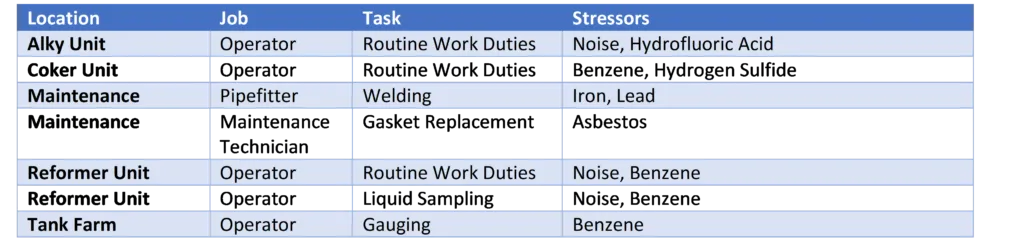
Table 1: Similar Exposure Groups (SEGs)
Step #2: Define Your QEA Strategy/Formula
After 30 years in the field of IH, I have seen some companies spend years perfecting their QEA model. Some spend a lot of time modeling their QEAs around variables such as frequency, duration, control technology factors, vapor pressures and even particle size distributions. These can be useful variables, but most companies do not have the resources or expertise to be that thorough — especially when just beginning their QEA program.
Just like when setting up your SEGs, you need to avoid ‘analysis paralysis’ and just start the process. After you’ve established your baseline assessments and have years of data to help validate your model, you may find it necessary to change your QEA model by adding additional variables that provide an even more precise assessment. Until then, start simple.
AIHA has developed a simple model that we recommend to our customers when they initiate their QEA programs. The formula is:
Risk Rating = Exposure Rating X Health Effect Rating
Common ratings used for these variables can be seen in Table 2 below:

Table 2: AIHA: A Strategy for Assessing and Managing Occupational Exposures, 3rd Edition
Step #3: Conduct Your QEAs
Break up Table 2 so each SEG and stressor are listed in a unique row. Then, add columns for your Exposure Rating and Health Effect Rating variables, and one column for the calculated Risk Rating. Table 3 below shows how to apply the AIHA strategy for the SEGs identified in the Houston Refinery example.
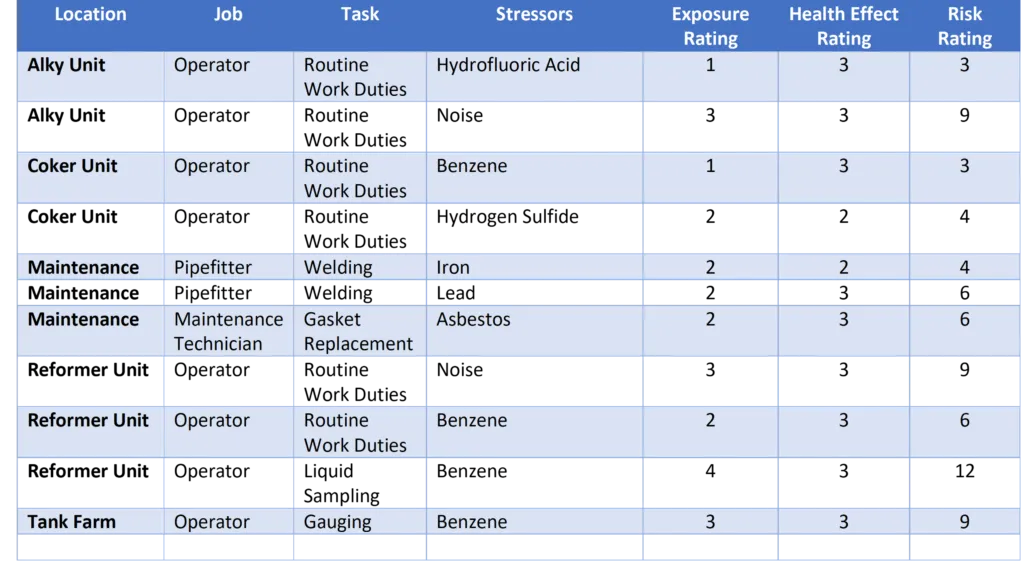
Table 3: QEAs for individual SEGs by unique stressors
Based on information in Table 3, we see the highest risk is the benzene exposure while liquid sampling by Operators at the Reformer Unit, while the lowest risks are benzene exposure to Operators at the Coker Unit when performing routine work duties.
Step #4: Display Your QEA Data in a Risk Matrix
The QEA in Table 3 shown above contains a lot of great data, but it is not recommended for use when presenting QEA findings to workers or management. Let me explain. It can easily become overwhelming and confusing when applied to a site containing 50-100 rows of data. Instead, we recommend summarizing the data using a risk matrix.
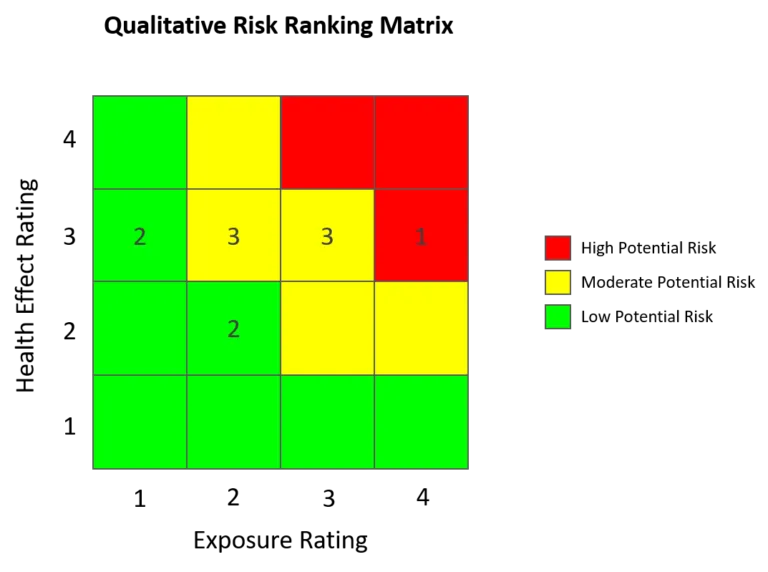
Risk matrices are already widely used by safety, quality and other departments across the organization to the status of their programs and related risks. So, why not use the same tools to convey IH information, right? Far too many IH professionals seem to believe they have to show a ton of complex data, statistics and fancy graphs to effectively communicate exposure risks. IH practitioners should, as a whole, get out of the “black box” mentality and simplify our messaging for both employees and management.
Risk matrices also take advantage of peoples’ existing visual and psychological cues. Let me explain. When presenting this data, viewers’ eyes will be almost instinctively drawn to the red items, right? They will inevitably ask:
- What’s the job/activity in red?
- Do we have data confirming the risk levels?
- How are we protecting these workers today?
- How do we move the risk from a red to a yellow, or even green?
By applying this familiar risk matrix, now we have an engaged audience—one that understands and wants to work with you to address those risks. I’ll tell you, a good manager really doesn’t like seeing red in any of the matrices they are responsible for.
I have used matrices just like this one to successfully grab the attention of management and secure approval for investment in workplace exposure controls. In several cases, these same controls were recommended for years by multiple EHS professionals, but only when making those risks easily visible and understood via the matrix did it get the attention from management it deserved.
Step #5: QEA Outcomes
After you and your stakeholders understand the exposure risks in the workplace, you can then begin an informed discussion about what to do. If the risk rating is low (green), you should track for potential exposure risk changes and no additional sampling may be needed. If the risk rating is moderate (yellow), sampling is likely needed and controls implemented (PPE, training, engineering controls, etc.). If the risk rating is high (red) this warrants immediate action (typically PPE to start – then engineering and other controls, medical surveillance, additional sampling, etc.). These actions and controls will be covered in more details in upcoming parts of our seven-part IH 101 series.
Next Time…
In Part 3 of our IH 101 series, we’ll explore how to utilize the data from our QEAs to identify where additional investigation and sampling is needed. You’ll then be able to produce a ranked list that can be used to best prioritize your resources and develop a sampling plan that’s laser-focused on providing you with information needed to improve the precision of your QEAs.
Other IH Program Resources
QEAs are just one of the many moving parts that make up an effective IH program. Your SEGs, sampling plans, lab analysis, data analytics and reporting systems, medical surveillance and program evaluation processes all deserve equal focus, and should be carefully coordinated to ensure optimum IH program performance.
Don’t forget to review our IH Program Cycle Infographic and IH Program Guide to help guide you through our IH 101 series.
In the Meantime…
VelocityEHS IH Solutions give you a software system that’s purpose-built to coordinate and maintain a comprehensive IH program founded on AIHA best practices. Designed by our in-house team of Certified Industrial Hygienists (CIHs), VelocityEHS IH Solutions help you easily assess and control workplace stressors, automate time-consuming IH program tasks, and maintain a world-class IH program no matter your level of IH expertise. Visit our IH Solutions Page to Learn More!
Ready to see for yourself how VelocityEHS can help you revolutionize your IH program? Contact Us or Request a Demo today!