In Part 5 of our IH 101 blog series “Data Analysis – Defining Your Goals & Selecting the Best Metrics“ we learned about effective tools for analyzing your IH data, and the critical importance of defining the purpose of your data analysis. Just generating a lot of statistics that don’t provide valuable insights is a waste of your time and resources. You must first define what your analysis goals are, then define the best statistics and tools to analyze your progress toward those goals.
If all of the statistics and analysis methodologies in Part 5 made your head hurt, you can relax. This article will focus on a topic that is much easier to understand: Medical Surveillance Programs (MSPs). Additionally, we’ll toss in a few golden nuggets to help you streamline the process if you have MSPs at your company.
Recommended Readings
Before you read on, we recommend reviewing the previous installments of our IH 101 Introduction to Industrial Hygiene Program Management series:
- Part 1 – Similar Exposure Groups (SEGs)
- Part 2 – Qualitative Exposure Assessments (QEAs)
- Part 3 – Sampling Plans
- Part 4 – Lab Analysis
- Part 5 – Data Analysis
We also highly recommend downloading our IH Program Cycle Infographic and IH Program Guide on the 7 steps to effective industrial hygiene (IH) program management to help you understand how each of these parts fit into the overall IH program management structure.
Medical Surveillance Program Basics
Before diving into best practices for MSPs, let’s first have a quick refresher of the basics:
What is a Medical Surveillance Program?
An MSP is defined as the set of medical activities that must be performed on workers when exposures to workplace stressors exceed a certain level. The program will list what the stressor of concern is, the threshold at which workers need to be tested, and the medical activities and their frequencies that need to be conducted.
Why are MSPs needed?
The purpose of the MSP is to evaluate workers exposed to stressors above a set threshold and quickly identify any adverse health effects early-on so they may be removed from the exposure before further damage to worker health occurs. IH program managers should be notified any time adverse health effects are discovered, while ensuring compliance with HIPPA privacy laws and any company privacy policies. IH can then use this data to target specific workplace risks for additional assessments and/or control measures.
For example, workers with an abnormally high level of blood lead level must be removed from the work environment causing the exposure immediately. IH should assess the hygiene procedures of workers and ensure they are using their PPE appropriately. Additional air monitoring and an assessment of other exposure controls may also be deemed necessary.
Who defines the requirements for MSPs?
Standards set forth by regulatory agencies such as OSHA are the most common source of MSP requirements. However, companies can establish their own MSP policies including health surveillance programs to manage risks from non-work related health conditions such as diabetes or high blood pressure. Regardless of the source of the requirement, an occupational health professional should be involved in defining the medical activities and their frequencies.
A great resource that summarizes the OSHA regulations for MSPs is their Medical Screening and Surveillance Requirements in OSHA Standards: A Guide.
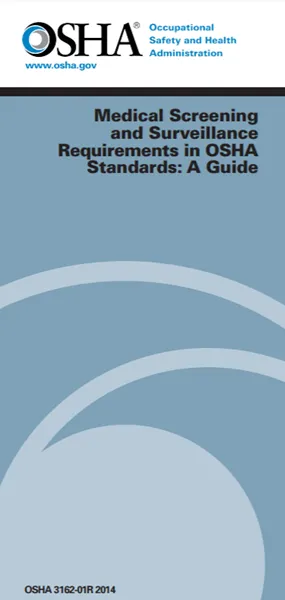
The guide provides a one-page summary of the OSHA MSP requirements for each regulated stressor. For additional information, you can also go to OSHA’s Safety and Health Topics Pages on:
- Arsenic
- Asbestos
- Benzene
- Bloodborne Pathogens and Needlestick Prevention
- 1,3-Butadiene
- Cadmium
- Carcinogens
- Chemical Hazards and Toxic Substances
- Cotton Dust
- Dermal Exposure
- Emergency Preparedness and Response
- Ergonomics
- Ethylene Oxide
- Formaldehyde
- Hazardous Waste
- Laboratories
- Lead
- Methylene Chloride
- Occupational Noise Exposure
- Respiratory Protection
- Silica, Crystalline
- Tuberculosis
Who needs to be included in medical surveillance programs (MSPs)?
Most regulations specify a threshold of exposure that, if exceeded, requires workers be placed into an MSP. Keep in mind that once there’s an exceedance, there are direct exposure controls and other actions that must be taken to minimize or eliminate the exposure and protect the worker. When it comes to MSPs, you are looking at the worse case exposures and not statistics.
Best Methods for Setup and Maintenance of Medical Surveillance Programs
There are a few fundamental steps necessary to set up and maintain your MSPs and ensure workers are enrolled in the right programs based on exposures:
Step 1: Define applicable MSPs and their required medical activities
Looking at your locations and assessment of potential exposures, you can determine which MSPs may be required under any applicable regulations. For example, a list of potential stressors at your locations may include noise, benzene and silica — all of which are regulated by OSHA and have MSP requirements.
Step 2: Define thresholds
For each MSP, determine the threshold level at which workers need be enrolled in that MSP. For example, noise exposure exceeding an 8-hour TWA of 85 dBA would necessitate enrollment in the MSP.
Step 3: Evaluate who needs to be enrolled in MSPs
For determining who needs to be enrolled, you can take a look at one or both of the following:
- Risk ratings – These are obtained through your qualitative exposure assessments (see Part 5). If the risk rating is above the threshold set by the MSP, all members of the SEG should be enrolled.
- IH Sample Data – At a minimum, all persons for which sampling shows exposures exceeding the defined threshold should be enrolled in the MSP. An important determination is whether to enroll all workers that do the same job (i.e. are in the same SEG) or to assess each worker’s potential exposure independently. Most professionals would apply the enrollment to the entire SEG. However, you may be able to justify individual worker enrollments/de-enrollments if you can reliably demonstrate that those workers experience different exposures due to unique work procedures, and can verify that samples taken on these individuals do not exceed the threshold.
Step 4: Automated Enroll and De-enroll of workers in MSPs
Manually updating the lists of workers that are enrolled and de-enrolled in MSPs is a time-consuming task. IH software can make this job not just easy, but virtually effortless. The key is to be able to get accurate employee data from your HR department and map it to the requirements for who needs to be included in each MSP.
The best method is to map HR information specifying workers’ jobs and locations on to each SEG. With HR data being continually updated in the background, workers will be moved in and out of SEGs automatically as job roles and locations change. If you define who is required for your MSPs at the SEG-level, workers will automatically move in and out of MSP enrollment as they move in and out of SEGs.
Unfortunately, there are limitations to most HR systems and records, and getting a 100% accurate, real-time account of all workers’ job roles and locations is very difficult. That being said, even a 50% automation of MSP enrollment saves enough time and resources to make it worth the effort.
Other IH Program Resources
Setting up and maintaining your MSPs is just one of the many moving parts that make up an effective IH program. Your SEGs, QEAs, sampling plans, data analysis and program evaluation processes all deserve equal focus, and should be carefully coordinated to ensure optimum IH program performance.
Our certified IH experts have developed two new complimentary resources – the IH Program Cycle Infographic and IH Program Guide which will introduce you to a proven, process-based IH program management framework built around continuous improvement principles and AIHA best-practices. Download them today!
We’ll also be hosting a series of IH webinars where you’ll get an in-depth look at each of the elements of a successful IH program, and have all your IH questions answered. Click Here to Register Today!
In the Meantime…
VelocityEHS IH Solutions give you a software system that’s purpose-built to coordinate and maintain a comprehensive IH program founded on AIHA best practices. Designed by our in-house team of Certified Industrial Hygienists (CIHs), VelocityEHS IH Solutions help you easily assess and control workplace stressors, automate time-consuming IH program tasks, and maintain a world-class IH program no matter your level of IH expertise. Visit our IH Solutions Page to Learn More!
Ready to see for yourself how VelocityEHS can help you revolutionize your IH program? Contact Us or Request a Demo today!