Ask most safety professionals, and they’ll tell you: Our goal should be to prevent incidents before they happen. But ask them how, and you’ll probably get many different opinions. It’s fair to say that in the absence of a coherent strategy, many fall back on the reactive approach of addressing risks only after incidents have occurred. But luckily, the Prevention through Design (PtD) framework gives us a sound basis for identifying and addressing risks at the design level, freeing us up from the constant need to respond to incidents and helping us become more proactive.
In what follows, we’ll give an overview of types of risks in the workplace, and how a PtD framework can give us the higher-level view and management of risks we need to prevent incidents before they happen.
Types of Risk
First, let’s start with the most basic question: What is risk? A good resource to help with that is ISO 45001, the global standard for Occupational Health & Safety (OHS) management systems.
ISO 45001 defines risk with almost Zen-like simplicity as an “effect of uncertainty.” In a note beneath the definition, the Standard elaborates that “risk is often characterized by reference to potential “events” and “consequences”, or a combination of these. The “combination” idea leads to the concept of a risk matrix, in which the overall ranking of risk is a product of its likelihood and the severity of outcome. In the matrix below, the most significant risks are those in the red zone in the top right corner.
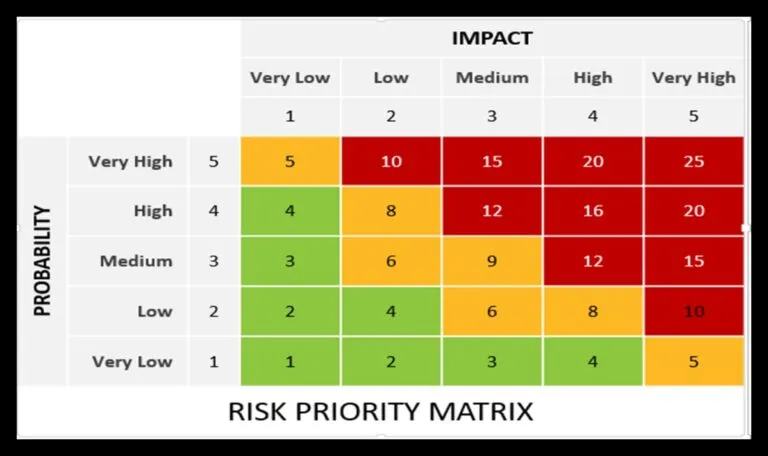
An important point here is that risks arise from many different sources, or hazards, and come in many different varieties. For example, risks can result from physical hazards like chemical exposures or machine pinch points, from human factors such as risk perception or risk tolerance, or from operational factors such focus on production goals and lack of an effective safety culture.
We can categorize risks by their primary effects, and some will be significant enough to check the box across all categories. A catastrophic chemical release would be an occupational safety risk (to our own workers), an environmental risk (to air/water/land), a regulatory risk (safety and environmental regulations), a legal risk (because of potential civil suits), a financial risk (because of potential fines/lawsuits), and a reputational risk (because of news of the incident)
The PtD Framework
One of the major problems affecting safety performance is that many processes, facilities and workstations were designed with production and functionality in mind, with little or no consideration of safety and environmental risks. EHS professionals then must spent considerable time and resources after the fact trying to retrofit safety and environmental controls, and even then, the solutions will never be as optimal as what we’d have had if EHS was considered in the design phase. And we often don’t learn these risks exist until after an injury has happened. Multiple studies have found that many 20% or more of all injuries and over 60% of fatal injuries occur because of design decisions.
Growing recognition of this problem led National Institute of Occupational Safety and Health (NIOSH) to develop the Prevention through Design (PtD) initiative. According to NIOSH, the mission of PtD is “to prevent or reduce occupational injuries, illnesses, and fatalities through the inclusion of prevention considerations in all designs that impact workers.”
The five principles of PtD are:
- Address EHS as early as possible in the project: The sooner we can identify potential health, safety, and environmental hazards associated with our plans, the sooner we can explore alternatives, and plan controls for residual risks.
- Identify and consult all relevant stakeholders: Our ability to execute principle (1) effectively depends on this. We need all relevant stakeholders at the table, including people associated with construction, operations, and maintenance, and utility company and municipal government representative, as applicable.
- Make construction process knowledge available to decision makers: This is necessary but often difficult, because communication is often fragmented across construction stakeholders involved in initiation, design, production, use and maintenance of facilities.
- Implement the hierarchy of controls in decision making: The goal of PtD is obviously to eliminate or substitute out exposures to risks whenever possible, because that’s always going to be the most effective strategy. Where we can’t do that, we need to use administrative and work practice controls, and personal protective equipment (PPE) as a last resort, to control residual risks.
- Review and continuously improve: As we move forward with our plans and identify previously unanticipated hazards or implementation issues, we need to revisit and revise our plans.
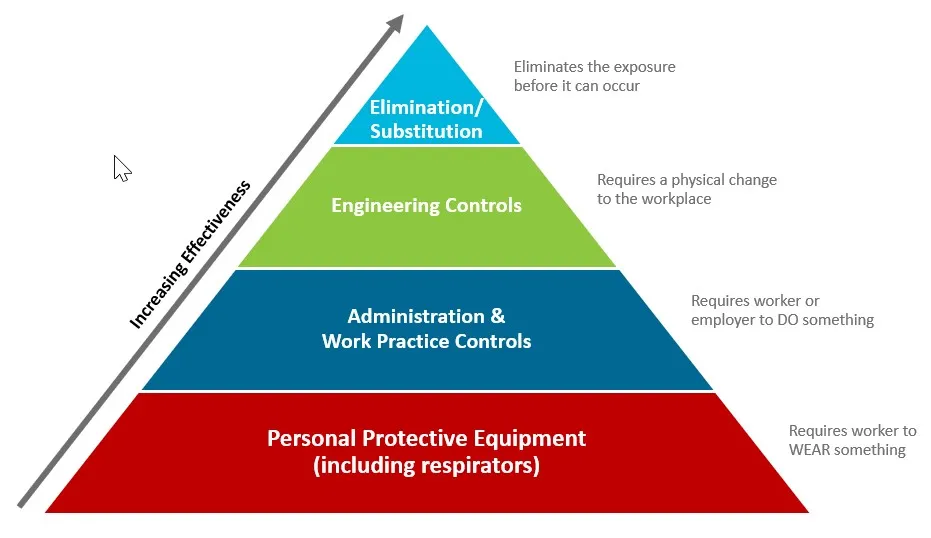
For example, suppose we’re designing a building that will have solar panels on the roof. We’d need to make sure we were designing the roof with the future solar panels in mind, including safety considerations for workers who’d be doing the installation and also maintaining the solar panels in the future. That means, among other things, that we’d want to design the roof to have a slope optimal for long term use of solar panels, and ensure there’s enough of a distance between the panels and the roof edge to allow safer passage of installation crew, and for passage of any personnel involved in later maintenance of the panels.
The great thing about a PtD framework is that it’s general and flexible enough to allow us to use it in many contexts for many different categories of risks. For example, we can use it to assess the risks of new chemicals we’re considering for use in a planned process line, and identify ways to substitute less hazardous chemicals. We can also plan how to build workstations with fewer ergonomics risk factors, such as potential for musculoskeletal disorders (MSDs). The better we get at using PtD, the more success we’ll have in expanding its use, and improving our safety management system.
Total Worker Health ®
A PtD framework can also help us get better at recognizing psychosocial risks, which are risks due to anxiety that workers feel because of their jobs, including known safety risks at work. This anxiety can also increase risks for other types of injuries, whether because of distraction or because of the muscle tension that results from stress, which increases risk of MSDs. Better recognition of and control of risks starting with the design phase can go a long way toward reducing anxiety levels.
An increasing focus on what NIOSH calls “Total Worker Health” ® was already in motion before anyone had even heard of the SARS CoV-2 virus, but the pandemic has certainly accelerated awareness of its importance. The work environment itself is evolving with more multi-employer worksites, temporary workers, and geographically isolated work. Safety professionals will need to carefully balance these issues to meet the challenges and opportunities presented by the future of work.
Leading Indicators (LIs)
We’ll only be effective in preventing workplace safety incidents if we’re effectively measuring our past performance, as well as the actions we’re taking to prevent future incidents. We record our historical performance using lagging indicators such as total incident rate, recordable injury rates, and Days Away, Restricted or Transferred Rate (DART). Both leading and lagging indicators are important to track, because as the saying goes, you don’t know where you’re going until you known where you’ve been.
Most people are already doing pretty well when it comes to lagging indicators, in part because some regulations such as OSHA’s Recordkeeping Standard require employers to track certain lagging metrics. But employers don’t often do as well as they could be doing on their leading indicators.
For example, do the leading indicators we’re tracking directly tie in with safety and management goals? Leading indicators need to be relevant to give us the benefits we’re hoping for. For instance, if we know that we’ve had a pattern of injuries due to trips/falls in a certain area, and investigations have revealed the cause to tools and packaging material blocking walkways, one leading indicator we can track might be the number of inspections of the area that do not find obstructions in place. Collaborating with our workers on all aspects of safety, from incident investigations to leading indicator selection and tracking, helps ensure we’re getting the information needed to monitor our progress.
Bringing It All Back Home
This brings us to an important point. Safety can’t be one-person job, or a job relegated to people with the term “safety” our “EHS” in their job title. Safety efforts need to be collaborative processes if they’re going to work. That means we need all of our people involved in helping us to identify risks, develop controls, assessing whether the controls are effective, and capturing the data needed to measure our performance and assess whether anything in our approach needs to change. Of course, as the nature of work itself continues to evolve, safety professionals may find that it’s challenging to keep pace and keep everyone connected to their safety programs.
Software can help us to continue evolving in step with the challenges and opportunities of the modern workplace. For example, Safety software can help us share responsibility for key safety tasks like incident management, safety meetings, inspections and observations, training, and actions management, while making it easier for all our workers to access safety data sheets (SDSs) for information about the hazards of chemicals they work with. With configurable dashboards and simple reporting features, we also can make sure we have the data we need to drive better safety management, including access to the leading indicators most important to our business.
Operational Risk software can also help by giving us a comprehensive view of risks in our organization, from potential causes of unplanned events, to possible consequences and severity of outcome, to visibility of the controls we have in place and their real-world effectiveness. A simplified bow-tie analysis tool can help us get our employees directly involved in the process, and help us to more efficiently onboard them and keep them aware of changes to our risk management system as elements of our operations change.
Preventing incidents is everyone’s responsibility, but it’s our job as safety professionals to make sure that “everyone” is really included. Software can give us the means to have a truly integrated and inclusive approach to safety that helps us become more proactive, and protects the safety and well-being of all our workers.
Let Velocity EHS Help!
VelocityEHS knows that people matter when it comes to safety, so we’ve made it easy for you to stay connected with yours. Contact us today to learn more about our Safety solution and Operational Risk solution can help you become more proactive, safe and sustainable.