Welcome to the second installment of our blog series “Introduction to EHS Risks,” in which we’ll break down how to prioritize your risks using a tool called the risk matrix. In case you missed our first installment, take some time to check it out for an overview of EHS risks, and to learn why you don’t need to have a big company or facility to benefit from better risk management.
Now, let’s talk about how to prioritize your risks, and why it’s such a central part of your risk management program and your job effectiveness as an EHS professional.
The Challenge of Managing Risk
First, let’s set the stage with a quick review of the challenges of an EHS professional, which we discussed in greater detail in our first installment in this series. Many people in the EHS management world find they have a list of tasks that never gets any shorter, and often find themselves brought up short when a workplace accident belatedly reveals risks that had been there all along.
Better risk management can help with both of these issues First, it can help you better focus your time by making sure you’re concentrating on the most important things – namely, those job tasks and aspects of the workplace that have the largest associated risks to your employees and your business. And secondly, by doing that, you’re proactively identifying risks before they can surprise you, and your employees, by causing an injury or other major unplanned event.
Of course, the complicating factor is that there are many sources of EHS risks, as we discussed in our first installment. With all of those risks to contend with, how do you figure out where to start?
The Risk Matrix
Enter a tool called the Risk Matrix.
Recall that in our first installment of this series, we introduced the idea that a common way of thinking about risk sees it as a combination of the “consequences of an event and its associated likelihood,” to borrow a definition from ISO 45001, the international standard for occupational safety and health management systems.
In other words, risk is partly about the probability of something bad happening, and partly about the severity of outcome if it happens. It follows that a logical way to measure risk for a specific undesired safety outcome might involve giving it a ranking based on the product of its likelihood and its severity. An easy visual way to express this idea might be using a graph, that plots a measure of event likelihood on the “y-axis” and a measure of consequences on the “x-axis.” Then, by taking a quick look at the graph, we can easily spot the events that have the greatest combination of likelihood and consequence severity by their place on the graph.
That’s basically how a risk matrix works. It’s a visual way of prioritizing risks that makes it easy to see (quite literally) what your biggest risks are. Let’s see how it works by taking a look at the image below.
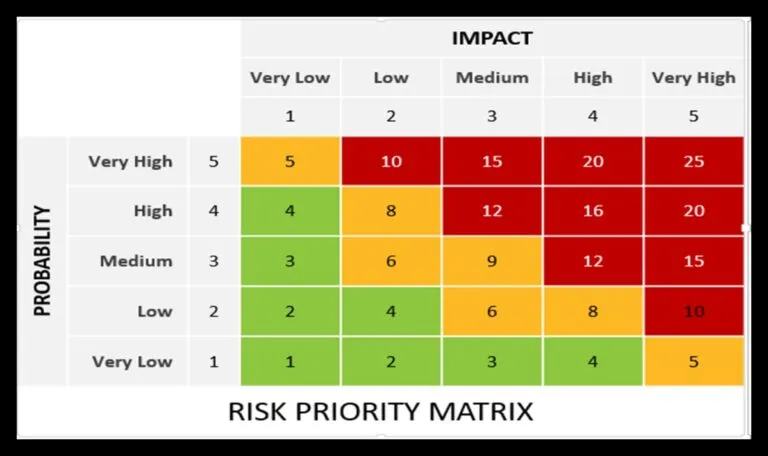
As we can see, the matrix gives us a great deal of information in a single glance. Probability of a safety incident is measured along the vertical direction of the chart, and severity of impact is measured along the horizontal direction. Risks with the greatest product, or combination, of probability and severity of impact wind up in the top righthand corner of the matrix. Both the red color (widely recognized as signifying a concern) and the “very high” rating tell us that this section contains our greatest risks. The yellow-coded middle of the chart, running diagonally, contains our intermediate-sized risks, and the green-coded section on the lower left side contains our smaller overall risks.
How the Risk Matrix Helps Manage Risk
The great thing about the risk matrix is that it’s both widely applicable and widely understood.
It’s widely applicable because you can use it to prioritize all of your EHS risks, no matter their source. That’s good news, since as we’ve seen, you have many sources of EHS risks.
It’s precisely because the risk matrix is such a universal tool that it’s also so readily understood. Just about everyone in the safety world uses them, so just about everyone understands them –they’re the lingua franca of the safety world.
For example, let’s say we’re looking for a better way to prioritize and manage our industrial hygiene risks. Industrial hygiene (IH) is a broad discipline that encompasses ergonomics as well as exposure to various workplace stressors, but for the sake of simplicity, in this sample matrix we’ll focus on risks of exposure to indoor air contaminants.
A widely accepted way of measuring such risks is by conducting qualitative exposure assessments (QEAs). A QEA is just estimation of the potential health risks for an individual employee, or for a similar exposure group (SEG) which, as the name implies, is a group of employees who have similar levels exposure to the same indoor air contaminants under the same conditions. You may already have sampling data for some of your SEGs to help you with quantifying exposure risk, while in other cases you may lack hard data and need to assess risk through other methods, including your best professional judgement.
The end result of your QEAs is a risk ranking you can summarize in a table, as shown below.

We can see that there’s a lot of great information there. But the problem is that the sheer amount of data can become overwhelming. If you have a large facility with many employees and a great deal of risk data to manage, a table like the one above can grow to contain 50-100 rows of data, and it can quickly become difficult for you and your employees to identify important trends that provide actionable intelligence.
Now, let’s see what such data might look like in the form of a risk matrix.
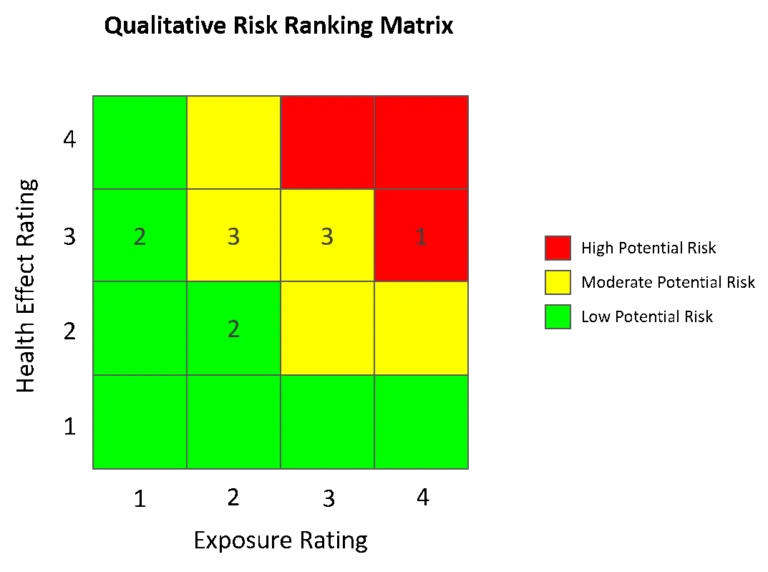
We can see that the risk matrix above helps us simplify our messaging for both employees and management. Anyone can look at the matrix and glean key information about how many risk rankings are high, moderate, or low, and the color coding of green/yellow/red is clear and intuitive.
Another advantage is that since risk matrices are one of the most common risk measurement tools in the EHS world, it allows you to consolidate your methods of ranking risks. You don’t need to have separate ways of presenting risk rankings for different kinds of risks from different sources, with the potential for confusion and inefficient management that brings. For example, you can use risk matrices to prioritize risks of slips/falls, risks of chemical spills/releases, or risks of musculoskeletal disorders (MSDs). All of this is even easier if you have the right EHS software, like a Risk Management solution to simplify identification and oversight of all your workplace risks, and an Ergonomics solution that uses artificial intelligence (AI) to identify MSD risks you might otherwise miss.
All of the advantages mentioned above bring another benefit: Improved engagement. Employees who work in areas impacted by the risks now have a better understanding of how to protect themselves, and a greater willingness to help further reduce risks. You’ll also find that company leadership will be motivated by the sight of risk ratings in the unseemly red part of the matrix. They’re going to want to get some of that red off their ledger.
And since you and your people only have so much time in the day, you need to make sure you’re focusing your efforts where they’re most impactful. The risk matrix gives you the clear intelligence you need to target the workplace hazards that create the most significant risks, so you can start have a measurable positive impact on your safety performance.
Additional Information on Prioritizing Risks
Looking for additional information?
Check out our on-demand webinar “Pitfalls to Avoid When Building Your Risk Matrices: An Honest Discussion with a VelocityEHS Risk Expert,” in which our own subject matter expert, Dana Garber, discusses strategies you can use to make sure you’re building accurate and effective risk matrices.
Watch our on-demand webinar (“Using AI to Assess Risk and Solve Problems in Manufacturing”).
As always, don’t forget to follow our Linkedin page for more updates about the worlds of EHS and ESG.
Let VelocityEHS Help!
VelocityEHS understands the challenges of risk management for EHS professionals in every industry. That’s why we offer Risk Management software that helps organizations of all sizes in all industries manage their risks. We can simplify the process of identifying all risks from all sources, managing risk controls, and engaging your entire workforce in risk management, so you can build and sustain the relationships needed for success.
Ready to see more? Visit our Risk Management page to request a demo with one of our solutions consultants today!