Last year, I was sitting at a table at the American Society of Safety Professionals (ASSP) annual conference in Chicago, eating lunch with fellow attendees when one of them asked me where I worked. I told him I worked for an EHS and ESG software company; he looked up from his deli sandwich for a moment and asked, “What’s ESG?”
Don’t feel bad if you share his uncertainty—ESG stands for environmental, social, and governance. The more we present at conferences and offer webinars on ESG, we find that many traditional EHS managers (a category which, for our purposes here, includes “safety managers” and other company representatives with “safety” in their title) either haven’t heard much (if anything) about ESG, or if they have heard of it, they assume it lacks relevance to them. They sometimes think ESG is only relevant to the investing world, meant for ranking of funds offered by investment services based on ESG performance. The irony is, we’re also starting to see uncertainty from other directions, as companies are hiring sustainability managers with little or no EHS experience, and more CFOs and CIOs are finding themselves pulled into conversations about ESG for the first time.
This is the reason for a new blog series, “Why Should ESG Matter to Me?” In it, we’ll present tailored arguments for different industry professionals who increasingly need to understand more about ESG to do their jobs effectively, even (and especially) if they don’t know that yet.
This first installment is for EHS managers who might know ESG exists, but don’t see what it has to do with them. In what follows, we’ll unpack the ways ESG connects to the things you’re already doing now, and how building ESG maturity can make those things easier.
Introducing ESG QuickTakes: A Sustainability E-Newsletter!
Master ESG with our NEW quarterly publication. Get expert insights on regulations, energy management, and sustainability delivered straight to your inbox.
What is ESG?
First, let’s cover some background on what ESG is, and its rising importance to companies around the world.
You’ve probably heard terms like “sustainability” and “corporate responsibility” before. The first often pertains to an organization’s efficient use of natural resources, and its active reduction of harm to the natural environment and to communities. The second term generally encompasses an organization “doing the right thing” – a concept that includes sustainability but also community involvement, ethical business practice and commitment to the greater good, rather than an exclusive focus on profit.
ESG includes and expands upon these topics, bringing in other stakeholder concerns, many of which have become recognized goals in global frameworks such as the United Nations (UN) sustainable development goals (SDGs). A synopsis of issues under the ESG umbrella includes:
Environmental: This category encompasses compliance with existing environmental regulations, including (in the US) EPA regulations such as the Clean Air Act, the Clean Water Act, Emergency Planning and Community Right-to-Know Act (EPCRA), and Resource Conservation and Recovery Act (RCRA), and associated requirements such as air and water permits, hazardous waste management, and chemical reporting such as Tier II reports and Toxic Release Inventory (TRI)/Form R reporting. It also includes measurement of greenhouse gas (GHG) emissions that contribute to climate change, whether or not they come from operations under the organization’s direct control (e.g. process emissions) or from utility consumption, or from offsite sources such as the treatment storage and disposal (TSDF) facilities that treat the facility’s waste. It should be noted that there’s a growing trend toward mandatory disclosure of GHG emissions and associated climate risk information, such as whether a company has implemented a climate transition plan, as evidenced by the Securities and Exchange Commission (SEC) 2022 proposed rule that would require climate-related disclosures from public companies. Plus, the environmental category includes the company’s efforts to reduce its energy and water consumption, reduce volumes of hazardous waste generated, improve its recycling and reduce amounts of waste sent to landfill, to reduce consumption of non-renewable resources, and to consider the broader ecological and environmental impact of its operations.
Social: This broad category basically pertains to how the organization treats people, whether they’re inside or outside the company’s walls. It includes compliance with safety regulations such as those issued by OSHA in the United States, as well as its following of industry best practices for safety. There is also a focus on human capital, which includes a wide range of practices related to its workforce, such as handling of labor issues and compliance with labor laws, psychological safety and management of psychosocial risks, and commitment to the continuing education and skills development of its workforce. It includes the company’s quality management process and how well it manages the safety of its products and services, and the company’s interaction with an impact upon its community and the world. The term social sustainability refers to the goal of building safe and healthy places, both inside and outside the workplace. A social sustainability focus might involve avoiding reliance on exploitative overseas labor practices, not sourcing raw materials from regions where the sourcing may contribute to political oppression, and consideration of the broader impacts of company’s operations, including the impacts of its waste generation and product life cycle on the environment and local communities. For example, your company’s hazardous waste generation may result in GHG emissions and other impacts to the environment and nearby communities when it is disposed of or treated.
Governance: This category is based around how well a company is managed and how well it abides by ethical practices at all levels. Some of the aspects covered in this category include compensation plans, including the gap between executive compensation and other employee compensations, and whether executive compensation is tied to achievement of ESG-related goals such as sustainability. Other considerations for governance may be compliance with applicable financial and tax regulations and the transparency of associated records.
In the sections ahead, we’ll review many common areas of EHS management, and in each case, we’ve seen how they intersect with areas of ESG, and how better management practices provide a good foundation for ESG maturity. Here’s a spoiler alert: We will see that do ESG well, you first need to do EHS right, but once you do, your ESG management helps you maintain your core EHS management system, as shown in the diagram of the ESG Pyramid below.
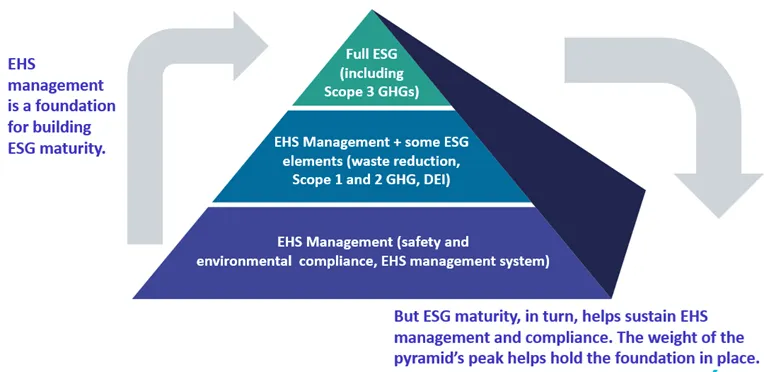
Keep this concept and this diagram in mind as you read on, because you’ll see this idea at work many times during the discussion.
Connections Between ESG and Safety and Health
Let’s be honest for a minute about one of the reasons many EHS professionals haven’t jumped onboard the ESG train yet. It’s because they believe, quite rightly, that they already have plenty on their plates, and don’t feel like there’s room for adding more. As a former Global EHS Coordinator myself, I know the general feeling very well – having a sizeable to-do list, and not enough time or help to get it done. I don’t blame anyone responsible for managing EHS for the lack of enthusiasm around having more work to do.
The good news is that ESG builds on all the things you’re already doing and makes them easier. Let’s look at a few specific areas of EHS management to see how they connect to ESG, and in turn, how getting better at ESG helps you maintain your core EHS management responsibilities.
Injury & Illness Management and Prevention
For better and worse, injury/ illness management is one of the first things that come to mind for most people, EHS managers included, when they think about the role of an EHS manager. I say “for better” because as a former Global EHS Coordinator myself, I believe the highest priorities of any EHS manager should be to make sure employees leave every day in the same condition as when they arrived for work, and to protect the environment. But I also say “for worse” because a singular focus on occupational injuries and illnesses often reflects poor performance at preventing injuries and illnesses and traps you in a “reactive” management cycle.
There are regulatory requirements to keep injury and illness records, such as OSHA’s Recordkeeping Standard in the US, Reporting of Injuries, Diseases and Dangerous Occurrences (RIDDOR) in the UK, and Canadian requirements established and managed by the various provincial Worker’s Compensation Boards (WCBs). These requirements weren’t created by the agencies involved to be just administrative tasks, or busy work. They’re intended to help you, as company EHS management, gather the information you’ll need about workplace incidents to understand why they happened and prevent future accidents.
Safety is part of the “S” (for “Social”) in ESG, along with compliance with labor regulations and social sustainability – a term used to describe efforts to build healthy and sustainable environments both inside and outside the company. Internal social sustainable efforts build upon, but also go beyond traditional safety management, to a focus on general health and wellness, and proactive identification and control of all risks, including psychosocial risks, which are sources of anxiety related to the nature of work or conditions in the workplace.
Ergonomics is a cornerstone of an effective safety management system focused on prevention, rather than just documentation of bad things that already happened. Ergonomics, of course, is the process of fitting the work environment to the worker. A central task in ergonomics is identifying and controlling potential for musculoskeletal disorders (MSDs), which are injuries to muscles, tendons, ligaments, joints, and nerves from overexertion, repetitive motions, or awkward motions. Common ergonomics assessment challenges include determining if you’re evaluating the right job tasks, and whether you’re accurately measuring body angles and force exertions.
One of the other benefits of ergonomics is its natural connection to other areas of ESG. For example, accessibility is a facet of social sustainability focused on creating a workplace that provides equal space and opportunities for all employees, across all aspects of personal identity including on race, gender, religion, and age. Because ergonomics by definition is about fitting the work to the employee, it’s an important part of recognizing the diversity of physical size and physical ability of populations of employees in your workplace and making sure your safety programs are accounting for that diversity.
Ergonomics tools using machine learning (ML) capabilities have been around for quite a while now, but they were cumbersome to use and labor-intensive to “train” to a point where they could provide users with meaningful insights. The best modern artificial intelligence (AI) based ergonomics tools are a different story. The model is up and running in days, without major interruptions to work and you can run the software from a mobile phone. You simply record the movements of employees as they perform job tasks, and the software, relying on embedded ergonomics expertise, provides you with useful information about ergonomics risks based on a few key inputs, like direction of motion, in addition to analysis of employee physical motions.
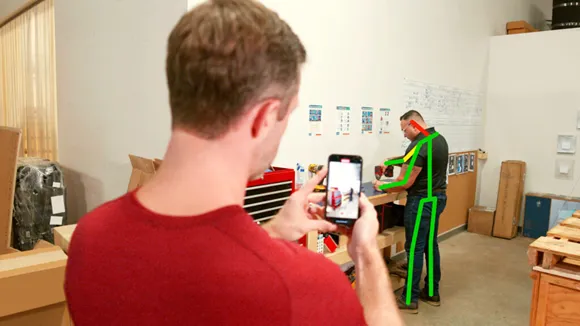
Best of all, the software then helps you prevent MSD injuries by identifying the job tasks with the highest ergonomics risks and helping identify root causes from expert-built lists for the specific MSD risks, which in turn helps you identify effective control measures. And your employees will be able to directly participate in the whole process, and will see the progress made for themselves, which in turn will help to promote better engagement with your safety management system and improve employee morale.
Chemical Management
Chemical management is one of the areas of EHS that even people outside the industry recognize as a key issue. We’ve all seen the news reports of major chemical spills and fires, and we intuitively understand that chemical exposure in the workplace can be dangerous.
Regulatory agencies understand that too, which is why there are regulations like OSHA’s HazCom Standard in the US and the Hazardous Product Regulations (HPR) and Workplace Hazardous Materials Information System (WHMIS) in Canada. These regulations require manufacturers and suppliers of chemicals to classify their products, and based on that classification, author safety data sheets (SDSs) and develop shipped container labels with the appropriate hazard communication elements, including specific hazard pictograms, signal words, hazard statements and precautionary statements. Employers, in turn, must use that information as the basis for their workplace hazard communication practices. They must provide barrier-free access to all SDSs for hazardous chemicals, ensure that all hazardous chemical containers are properly labeled, and provide their employees with training specific to the chemical hazards in their workplace.
HazCom management has some additional urgency at present, because OSHA is in the process of revising the HazCom Standard to align with Revision 7 of the UN’s Globally Harmonized System of Classification and Labelling of Chemicals (GHS). And Canada has already published a final rule updating the HPR and WHMIS to align with Revision 7.
Many chemicals also have Occupational Exposure Limits (OELs) that establish maximum concentrations to which employees can be exposed. Some OELs, like the OSHA Permissible Exposure Limit (PEL), are expressed as 8-hour time-weighted averages (TWAs), while values like Immediately Dangerous to Life and Health (IDLH), as the name indicates, represent exposures that could quickly overcome workers, and which employers cannot allow their employees to enter without a maximum level of respiratory protection.
These chemical management challenges are central to good EHS management and regulatory compliance, and of course, the safety of your entire workforce. You might not have thought of chemical management as part of ESG, but as we’ve discussed, safety is part of the “S” in ESG, so you’re already doing some of the things needed to build ESG maturity.
Better chemical management practices based on green chemistry can help you improve your performance by making it easier to choose safer and more sustainable chemicals, so you’ll have fewer chemicals with OELs that pose significant exposure risks to your employees. And the fact that your employees know you have better chemical intelligence integrated into your procurement process will improve their psychological safety and their engagement with your EHS programs.
Connections Between ESG and Environmental Compliance
Our discussion of chemical management above is a good primer for discussing environmental compliance, since chemicals we bring onsite often enter one or more environmental pathways, whether they’re released to air or water or being disposed of or treated as waste. This means these choices are part of the “E” (for “Environmental”) in “ESG,” which once again shows that when you’re managing these aspects of EHS, you’re already doing some work in ESG.
Let’s explore each of these pathways in more detail, examining how a more deliberate approach to building ESG maturity can reduce your compliance obligations and management burdens.
Air Emissions
Your processing of chemicals on-site often results in air emissions from particulate matter or vapors generated. These emissions can either be fugitive emissions if they are incidentally released to air or stack emissions if they are captured and directed to the outdoors via an exhaust stack.
Regulations such as the Clean Air Act (CAA) in the US require permits for many air emission sources, with more compliance-intensive Title V permits required for Major Sources with 100 or more tons per year of emissions of most regulated air pollutants, although lower thresholds apply in “non-attainment areas” not meeting National Ambient Air Quality Standards (NAAQS). But for chemicals included on EPA’s list of hazardous air pollutants (HAPs), EPA has lower Major Source thresholds of 10 tons/year of any individual HAP or 25 tons/year of combined HAPs. This means you’ll need to know which chemicals in your inventory are listed HAPs that would add to your regulatory obligations.
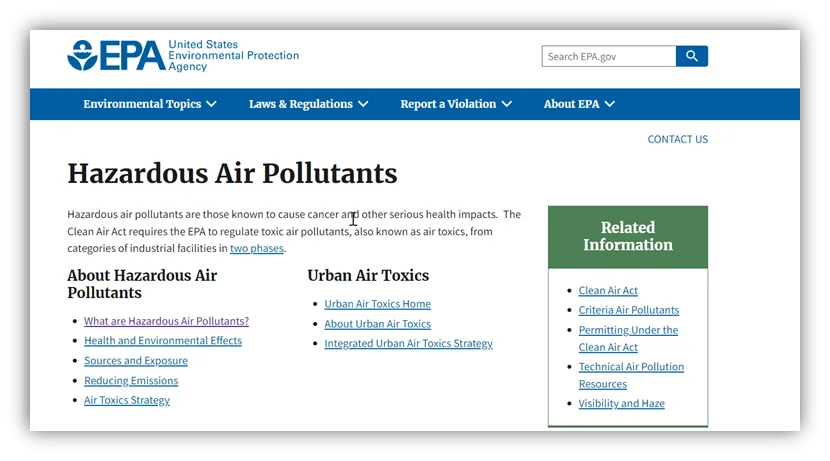
Understanding and reducing your emissions inventory will not only help you avoid permit exceedances and other potential violations but may also reduce your existing compliance obligations. For example, by using modern green chemistry tools to choose alternatives to HAPs, you can potentially drop down from Major Source status, revise your permit conditions, and significantly reduce your compliance burden.
Better air emissions management also improves your stewardship of the environment and your community, which is an increasingly important aspect of ESG. This is especially true because economically disadvantaged communities often are the most impacted by all manner of pollution including air – a fact acknowledged by European Financial Reporting Advisory Group (EFRAG) in its ESG standard ESRS S3 on “Affected communities,” which will soon be mandatory for about 50,000 EU companies. ESRS S3 will require covered companies to provide information about the ways they’re “working to prevent, mitigate and remediate the negative material impacts on affected communities” or achieve “positive material impacts” for those communities. Similarly, in the US, EPA has been focusing more on “environmental justice,” including the systemic impacts of pollution on the most vulnerable communities.
Water Discharges
Depending on your operations, some of the chemicals you bring onsite may also end up discharged to either industrial wastewater or stormwater. Many government agencies regulate water discharges. In the US, the Clean Water Act (CWA) gives EPA the authority to set standards for protection of water quality, and EPA requires permits for point sources of industrial stormwater and wastewater through its National Pollutant Discharge Elimination Systems (NPDES) program.
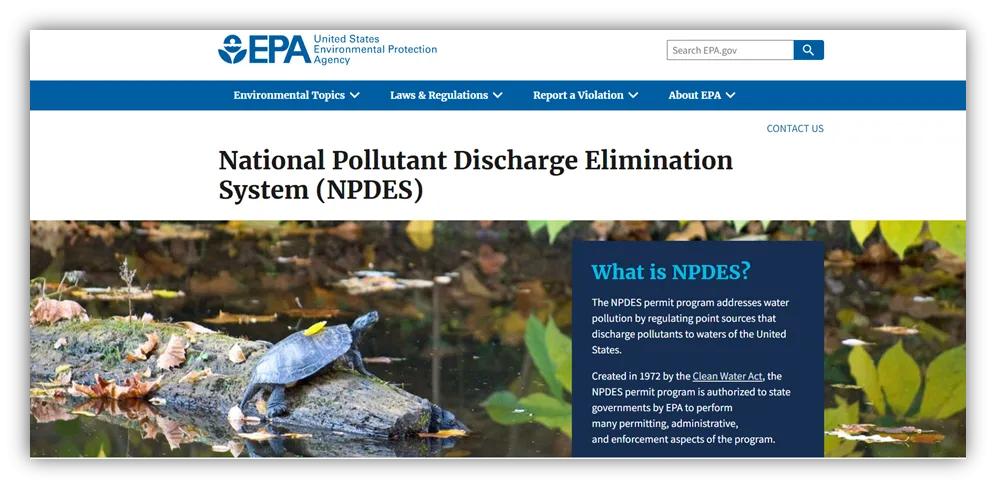
EPA maintains a list of 65 pollutants in general categories like “chlorinated benzenes” on its Toxic Pollutants List, which EPA considers when developing national discharge standards such as effluent guidelines or NPDES permit requirements. But an arguably even more important list to know about is EPA’s Priority Pollutants, which includes 126 individually named chemical pollutants for which EPA has published analytical test methods. The list of Priority Pollutants more directly affects the limits EPA established for permit conditions in its NPDES program.
Just as we saw with air emissions, better chemical management can lead to significant improvements. Green chemistry tools can help you avoid use of chemicals leading to discharge of regulated water pollutants, so you can stay within your permit limitations and even potentially reduce your compliance obligations. Since local communities may depend on water sources impacted by your discharges, and water pollutants in your discharges can adversely impact aquatic life and biodiversity, your ability to make safer chemical choices will also reduce impacts on the environment and local communities.
Waste Management
Many of the chemicals you process become wastes, which ultimately require treatment or disposal. But not all waste is equally dangerous. Hazardous waste poses significant potential for harm to human health or the environment. In the US, EPA regulates hazardous wastes through the Resource Conservation and Recovery Act (RCRA) and gives generators of wastes the responsibility to manage their wastes from “cradle to grave.”
Generator responsibilities start with identifying which of their wastes are hazardous based on RCRA criteria. Waste can be hazardous if it is included on one of four specific EPA lists (F, K,P and U), or if it has specific characteristics, such as ignitability, corrosivity, reactivity, and toxicity. EPA establishes parameters for these characters, such as flash point in the case of ignitable waste. Flash point is defined as the minimum temperature at which a liquid can evolve enough vapors to create an explosive mixture with air. EPA considers a waste with a flash point below 140 degrees Fahrenheit (deg F) to be ignitable, and therefore hazardous.
Of course, it’s not enough to just determine if you generate hazardous wastes. You then need to determine how much hazardous waste you generate per month, which is how you’ll find your generator status according to EPA. This is an important step because your compliance obligations depend on your generator status, as shown in the chart below.
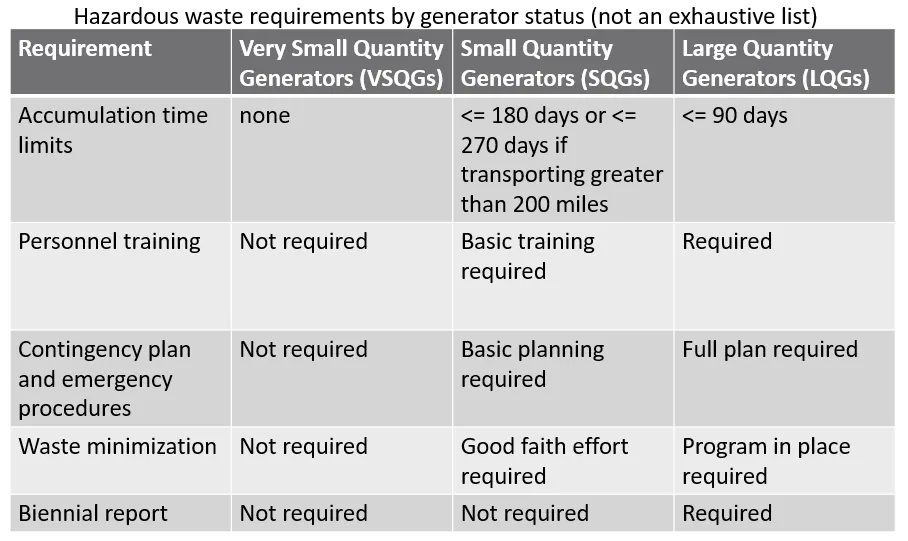
Many hazardous waste management strategies seem to center on operational changes to reduce quantities of waste generated, or to improve efficiency, such as streamlining waste tracking and reporting. Modern Environmental Compliance software can certainly help there, by making it easier to manage your waste profiles, access and review your waste manifests across multiple shipments, and easily complete your hazardous waste reports.
But why stop there? Start thinking in terms of the big picture, and exploring ways to make better choices about the chemicals you use, so you have fewer chemicals that become hazardous wastes in the first place. Using modern green chemistry tools, you can choose safer and more sustainable chemicals, reducing your hazardous waste generation right at the source. And with good gatekeeping processes in place and a reduced generator status, you’ll also have fewer regulatory obligations, so you can concentrate more on leading with best practices instead of being led by the compliance calendar.
Multimedia Environmental Reporting
In the US, Toxic Release Inventory (TRI), aka Form R reporting, is one of the most common and time-consuming reporting obligations. If a facility meets reporting applicability criteria based on their NAIC code and the quantities of TRI-listed chemicals they manufactured, processed, or otherwise used during a calendar year, they need to complete and submit a report to federal and state EPA authorities by July 1 of the following year.
For every chemical that exceeds reporting thresholds, you’ll need to calculate, and report amounts of the chemical involved in specific activities such as on-site waste treatment, off-site waste treatment, fugitive or stack air emissions, or water discharges. You need to perform a giant “mass balance” on your whole facility – reconciling the total quantities of chemicals you bring on-site with the quantities that end up in your products, are disposed, or are discharged to air and water. It also means that if you don’t have an easy way to track your air, water, and waste, you’ll have a tough time meeting your TRI reporting requirements.
There are requirements like TRI in other regulatory jurisdictions as well. For example, National Pollutant Release Inventory (NPRI) reporting in Canada is roughly analogous to TRI reporting, with applicability in part based on a regularly updated list of NPRI-reportable chemicals. You need better visibility into the chemical ingredients in your products to be able to meet your reporting obligations. But once you further improve that visibility with green chemistry tools, you can also potentially avoid the use of chemicals subject to reporting requirements such as NPRI and TRI and reduce your reporting burden as well as your impact on the environment.
Starting Your EHS to ESG Journey
Early on, when we introduced the idea of the ESG Pyramid, we noted that while EHS management is essential for doing ESG right, ESG maturity makes it easier to keep doing EHS right. We’ve seen this trend in some of our discussions of specific areas of ESG above, such as air emissions and waste management. Just as a reminder, here’s another look at the ESG Pyramid.
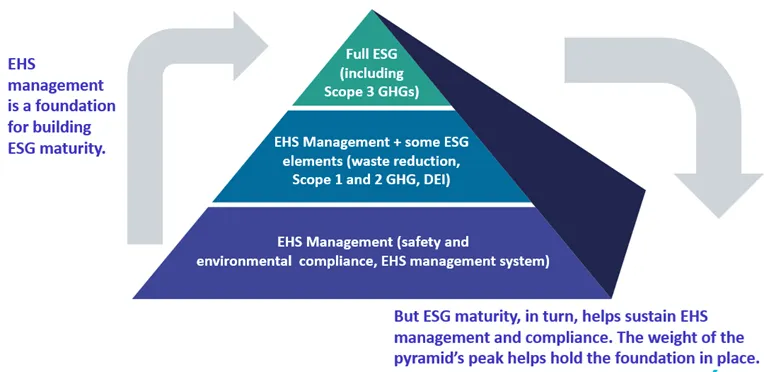
You need to find ways of simplifying your ability to access and use data to maintain regulatory compliance and have any chance of building ESG maturity. But as you become more mature using green chemistry capabilities, you can actually improve your selection of chemicals and reduce compliance obligations. And when you combine that with other ESG capabilities, like the ability to track all three scopes of greenhouse gases (GHGs), you’ll not only achieve EHS and ESG excellence, but also make excellence sustainable.
Looking for More Information?
If you’re looking for more information about starting your EHS to ESG journey, we’ve got you covered.
To learn how an environmental management system (EMS) based on ISO 14001 can be a useful framework at all points during your EHS to ESG journey, download our eBook, “An Overview of ISO 14001: Using the Standard to Improve Environmental Management.”
For an even deeper exploration of why ESG maturity helps you “weather the storm” during challenging times, check out our on-demand webinar, “Weathering the Storm: How ESG Maturity Helps You Maintain EHS Compliance in Challenging Times.”
Finally, for strategy on how to improve chemical management and chemical procurement processes, and how to leverage EHS & ESG software to support your initiatives, don’t miss our upcoming live webinar, “Using Chemical Management & Green Chemistry to Improve Your ESG Maturity & Value Chain Relationships.”
Let VelocityEHS Help!
We’ve built our entire VelocityEHS Accelerate ® Platform to help EHS professionals like you become safer and more sustainable. The Safety Solution helps streamline your most important safety management tasks, like incident management, inspections, follow-up actions, and maintaining and providing access to SDSs. The Green Chemistry solution builds on that by facilitating smarter choices of chemicals that pose fewer risks to your employees, communities and the environment and lighten your compliance burden. And the Environmental Compliance Solution can help you streamline management of air and water discharges and waste shipments and easily complete your TRI/Form R reporting.
You can move from a reactive to proactive safety management approach using AI tools to not only assess musculoskeletal disorder risks, but more importantly, get actionable, expert-curated insights to identify root causes and corrective actions with the Ergonomics Solution.
The ESG Solution provides exactly the support you need to track all three scopes of your GHG emissions, with reporting capabilities aligned with major ESG disclosure frameworks. Materiality assessment capabilities within the software also help you easily generate surveys you can share with stakeholders, so you be sure you’re identifying easier to miss issues such as categories of Scope 3 GHGs.
ESG is here to stay, so get the tools you need in place today to achieve and maintain ESG maturity. Request a demo or contact us today to learn more about how we can support your continuing ESG journey.