There are so many possible workplace hazards to assess, analyze, identify, and get controls in place for, both physical to psychological risks, that having the systematic approach of an operational risk management program is essential. With an operational risk management program, you’re better positioned to identify workplace hazards and get controls in place to mitigate them.
Your operational risk management program is a strategic framework that aligns with sustainable and responsible business practices. It provides a solid foundation to start integrating environmental, social, and governance (ESG) principles. By pulling ESG principles into your operational risk program you’re setting yourself and your organization up for long-term success, and it’s easier to do than you may think.
The “Step into ESG” blog series covers ways to incorporate ESG from existing programs such as safety, ergonomics, control of work, and health. This installment will explore how your operational risk program is already greatly contributing to corporate sustainability and what simple steps you can take to build and develop an ESG program for an even more sustainable future.
Why is ESG Important?
ESG continues to gain traction in the business world and is becoming harder and harder to ignore. Even if your organization isn’t required to report on ESG initiatives there’s a high probability that one or even many of your customers will face ESG reporting requirements. This means your customers may need to account for their value chain, in which case they could very well ask your organization to provide ESG reports so they can meet new regulatory requirements, as well as stakeholder expectations.
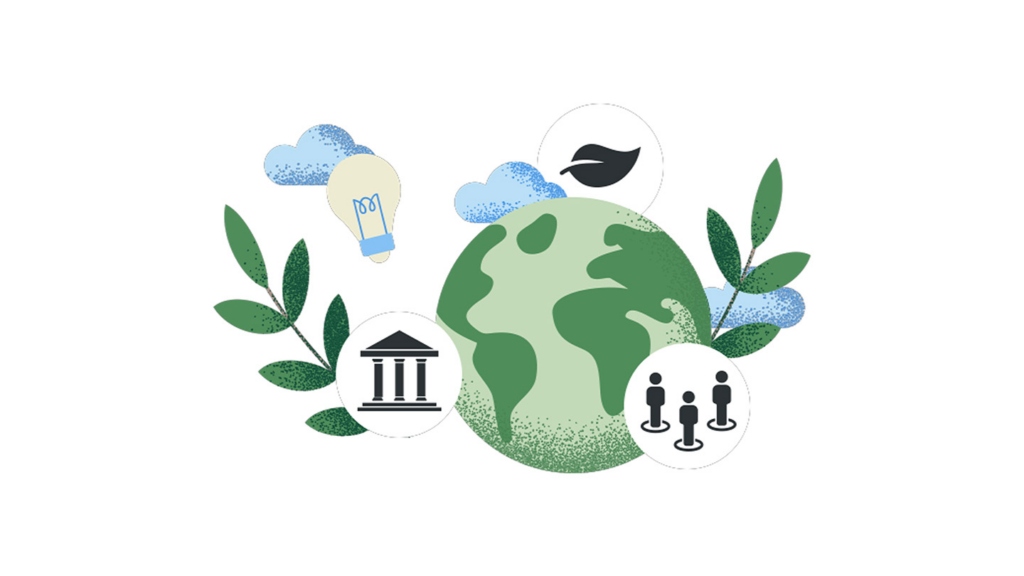
In addition to regulatory requirements, ESG has shown to give companies a competitive edge, reduce costs, improve profitability, and reduce risks, along with many other benefits. As an EHS professional, you’re in a position to have a huge impact within your organization if you use your operational risk program as a building block to integrate ESG into your scope.
Principles of Operational Risk Management
Operational risk management helps prevent incidents before they occur by assessing, analyzing, identifying, and controlling risk, along with verifying that risk controls are in place. Effective operational risk management programs allow you to collect essential data to help you make more informed decisions, allocate resources efficiently, and better navigate uncertainties and challenges while also maximizing opportunities for growth, long-term success, and a safer, healthier workplace.
Hazard Studies
There are many specific methods used for assessing risks, known as hazard studies, which include:
- Hazard Identification (HAZID)
- Hazard and Operability Study (HAZOP)
- Failure Modes and Effects Analysis (FMEA)
- Job Safety Analysis (JSAs)
- Process Hazard Analyses (PHAs)
- Layers of Protection Analysis (LOPA)
- Five Whys (usually done after an incident or event happens)
Hazard studies build the foundation of a safety culture by helping to systematically identify hazards before they result in an injury or create environmental risks or other unplanned events that might put your business, its reputation, and the community at risk.
Benefits of hazard studies include:
- More systematic visibility and control of risk
- Increased productivity, less downtime
- Improved employee morale
Bowtie Analysis
Another commonly used assessment tool is bowtie analysis. Bowtie analysis is a tool you can either start with, or you can create by pulling in information from hazard study assessments. It has the advantage of being visual and more easily understood and maps out a risk pathway—a causal flow from the causes of an incident to the incident, to its consequences.
A bowtie analysis makes it easier to see the controls you have in place such as:
- Preventive controls that stop an incident from happening, like a safety valve on solvent tank, which releases small amounts of vapor in a controlled way to prevent a possible explosion due to vapor build-up.
- Detective controls that tell you when something is happening, like a sensor that detects vapor from a release and sets off an alarm.
- Mitigative controls that reduce the impact of an incident or event happening, like a dike or berm around a tank that captures some of the liquid if the tank leaks or ruptures.
Assessing, analyzing, and identifying risks through hazard studies and bowtie analysis is just the beginning of a strong operational risk management program. Getting controls in place and establishing a critical control verification process, round out your program and create a safer more sustainable work environment.
Control Verification
A control verification process helps prove that the controls in place are working effectively and preventing risks. Plus, it’s a requirement under many international regulations and standards such as Australia’s Model Work Health and Safety (WHS) regulations, the UK’s Control of Major Accident Hazards (COMAH), and OSHA’s Process Safety Management (PSM) standard, among many others.
Control verification brings endless benefits to your operational risk management program. It gives your stakeholders more confidence, helps with process improvements, allows for more informed decision making, improves financial stability, and most importantly reduces risks in the workplace.
All these elements of operational risk management also provide a good foundation for building ESG. You’re already doing some of the work, now let’s see what simple steps you can take to implement or further mature an ESG program within your organization.
Introducing ESG QuickTakes: A Sustainability E-Newsletter!
Master ESG with our NEW quarterly publication. Get expert insights on regulations, energy management, and sustainability delivered straight to your inbox.
Connecting Operational Risk to ESG
Operational risk connects to ESG because both programs aim to prevent negative outcomes. They both rely on data to build and implement strategies that will help reduce risks while contributing to a more sustainable future. There are useful tools and strategies in both operational risk and ESG management that when combined can deliver incredible outcomes.
Hazard Identification and Monitoring
Hazard studies and bowtie analysis are valuable tools used in operational risk management to identify hazards in the workplace. You’re able to identify many different types of hazards so why not use these tools to help identify ESG risks and opportunities. For example, ESG bowties can be used to map out physical risks associated with climate change, or due to carbon pricing policies that may impact your organization’s profitability. These tools help breakdown where different ESG risks exist throughout the organization, opening the door to even more extensive risk management opportunities.
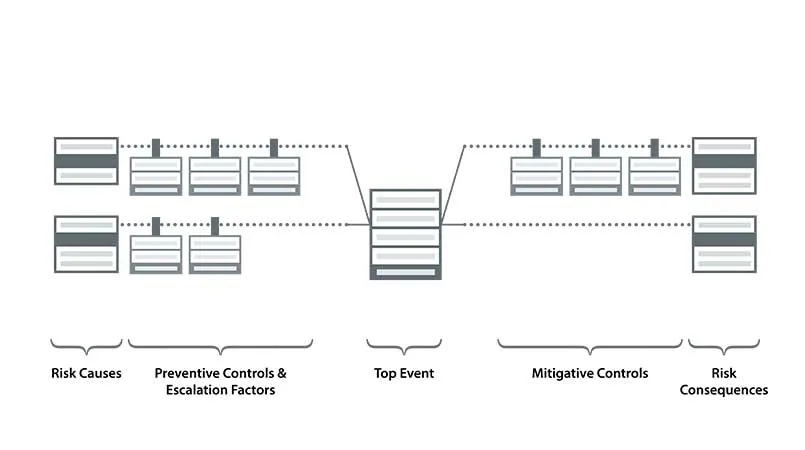
These operational risk tools are very useful, but you could gain even better insights by also using ESG tools such as materiality assessments. Materiality assessments are surveys of ESG issues that allow you to identify and prioritize the matters and risks that are most material, or important, to your organization and its stakeholders. A materiality assessment allows stakeholders to easily share their input, rank data by critical priority, and gives insight into both financial and global impact issues.
Knowing the risks that will have the biggest environmental and social impacts to your organization, inside and outside, will help you mature operational risk and ESG programs.
Employee Well-Being and Social Sustainability
Operational risk management plays a key role in improving employee well-being. The well-being of employees is primarily important because promoting well-being is an important goal in itself. Additionally, it contributes to your organization’s internal social sustainability, which is part of a mature ESG program.
Risk management ensures the health and safety of the people in your organization and helps foster a more positive work environment. It reduces psychological stressors, improves productivity, and helps build better engagement. When your team members know and understand controls are being put in place to reduce physical risks it naturally helps to reduce psychological risks.
This is because physical risks in the workplace causes anxiety, which is itself a health risk because it’s linked to health conditions like hypertension, but also because it increases potential for a workplace accident or injury. One way that can happen is distraction—an anxious team member isn’t as focused on the job and is more likely to make a potentially dangerous mistake. Additionally, anxiety causes tightening of muscles which can make someone more susceptible to an MSD injury.
You can even further reduce psychological risks by engaging your teams, allowing their voice to be heard and know it matters. Incorporating a materiality assessment into your identification process and including your team members as stakeholders in the assessment can help you understand exactly where their needs lie.
Better Management of Environmental Risks
Operational risk management also encompasses the scope of environmental risk controls and verifying these controls are effective. Incorporating ESG principles will give you better insight into how your organization can more successfully manage environmental risks.
Embracing ESG principles like monitoring your organization’s utility usage and greenhouse gas (GHG) emissions can help alleviate environmental impacts to the communities around your organization. This not only helps to reduce negative environmental impacts, but also promotes positive societal contributions, and helps avoid the kinds of reputational risks that affect companies who do not manage environmental compliance well.
Another ESG strategy such as green chemistry can be used to reduce internal environmental risks when it comes to chemical management. Green chemistry provides alternatives to hazardous chemicals to help reduce negative impacts to the environment and harmful health risks to the people in your organization.
Operational Risk and Governance
Keeping stakeholders informed and having a transparent operational risk management program allows for better risk control. Data collection and critical control verification help provide needed information for better governance and documents how well you’re managing risks.
Encompassing ESG performance into your operational risk reporting standards gathers information that business leaders and the investment community utilize to drive better business decisions. Nearly all large institutional investment firms use ESG information to analyze organizations because of the growing recognition that ESG data has real value in predicting business resilience. Additionally, value chain partners like transporters, distributors, retailers etc. increasingly want to work with companies that take ESG seriously, further reducing volatility to your business practices.
Being proactive and getting ahead of operational risks helps with long-term sustainability and business resilience in changing regulatory environments. Broadening the scope of your operational risk management program to include ESG risks will better prepare you to navigate the modern business landscape.
Looking for More Information to Help Guide Your EHS and ESG Journey?
To help with management standards the International Organization of Standardization (ISO) provides multiple standards designed for any organization. Both ISO 45001 and ISO 31000 help to reduce workplace risks and improve safety, while ISO 140001 helps with environmental performance, ISO 26000 helps with social responsibility, and ISO 45003 helps with psychological health and safety.
And don’t worry, VelocityEHS has plenty of resources available to give you even more information and expert insights to better manage your EHS and ESG programs:
- Webinars—Risk Management 101: Part 1, Part 2, & Part 3
- Webinar—Weathering the Storm: How ESG Maturity Helps You Maintain EHS Compliance in Challenging Times
- eBook—Introduction to EHS Risk: Why Risk Management is Central to EHS Management
EHS & ESG Thought Leadership Subscriptions:
You should also read about Velocity’s customers’ experiences. Like, how Dyno Nobel reported a 53% decrease in Total Recordable Injury Frequency Rate (TRIFR) with the Operational Risk Solution.
VelocityEHS has the Tools You Want!
Streamline and improve risk management with the Velocity Operational Risk Solution and award-winning ESG Solution. Gain unparalleled visibility and control of workplace risks, drive enhanced collaboration and engagement with your stakeholders, and adapt and scale to your organization’s needs.
Velocity offers multiple solutions that make it easier to manage, maintain, and ensure the long-term success of your EHS and ESG programs. The VelocityEHS Accelerate® Platform offers a single platform providing access to leading technology, expertise, and predictive management tools to help you proactively address workplace risks.
Discover more about how our solutions work together, talk to an expert today!