By Phil Molé, MPH
Welcome to the second installment of our blog series, “Why Should ESG Matter to Me?” In our first installment, we addressed the person in an environmental, health and safety (EHS) management role, making the case that Environmental, Social and Governance (ESG) builds upon all the things they’re already doing, and that building ESG maturity makes it easier to maintain core EHS management tasks.
This time around, we’re addressing Sustainability and ESG managers who may have been hired to manage sustainability initiatives, and possibly manage or initiate your company’s ESG process. Perhaps you came into your role without previous EHS exposure or experience. Or, perhaps you’ve been at this a while already, but don’t realize the extent to which the scope of ESG has expanded in recent years, and how much of that scope builds upon EHS management, especially higher-level knowledge and control of chemicals in your inventory. If so, this article is for you.
In what follows, we’ll help widen the frame on your role and responsibilities and demonstrate how your success as a sustainability and ESG professional depends on understanding EHS and developing good relationships with the people in your organization who manage EHS.
Introducing ESG QuickTakes: A Sustainability E-Newsletter!
Master ESG with our NEW quarterly publication. Get expert insights on regulations, energy management, and sustainability delivered straight to your inbox.
How ESG Connects to EHS
Right away, you should understand that our messaging in this blog will be a little different than in our first post, and probably in later posts, too. This series is called “Why Should ESG Matter to Me,” but ESG probably already matters to you because of your job description. So, we don’t need to convince you that ESG is important, but if you don’t have an extensive background in EHS, we might need to convince you that understanding the full context of ESG is important. Specifically, you need to understand that ESG done well not only builds upon, but depends upon, solid and sustainable EHS management practices.
You can see this more clearly if you think about what’s packaged within those three letters in “ESG:”
“E” (Environmental): This category includes many of the topics you probably already have top of mind, such as reducing your carbon footprint and greenhouse gas (GHG) emissions and reducing amounts of waste sent to landfill. But it also includes compliance with environmental regulations regarding air, water, waste, and chemical reporting. We’ll spend time in this article talking about those requirements and how they connect to and enable some of the higher maturity ESG management tasks in your role.
“S” (Social): This is a broad category that includes many of your company’s relationships with people, including workers in the whole value chain both upstream and downstream of your company, customers, and communities potentially impacted by your operations. But it also includes the employees in your workforce, as well as temporary and contracted workers under your supervision and goes beyond traditional occupational safety to include psychological safety and general employee wellness. Later in this article, you’ll see how to improve the effectiveness of your ESG program by embracing more proactive safety management practices that improve employee engagement with your safety management system.
“G” (Governance): In ESG parlance, “governance” or “corporate governance” is a shorthand term for how well a company is managed, and whether management has a “baked in” focus on ESG priorities, as evidenced by incentive plans for executives and formal policies. A big part of governance also relies on data – ensuring you have quality data to begin with, and that your reporting based on that data is accurate. Your job description likely includes responsibility for data and reporting, but as this article will later discuss, you’ll only be able to manage this task at a high level if you have a deep understanding of your EHS data, and efficient tools for collecting and managing it.
The messaging in our first post in this series was that to build ESG maturity, you first need to do EHS well, and we explained all of the reasons why that’s true. EHS management is the base of the ESG pyramid, as shown in the image below, and you won’t have a firm foundation for building ESG maturity without it. All this analysis still applies, but in your case, you’ve been tasked with managing the top of the ESG pyramid and need to connect those efforts to the base of the pyramid.
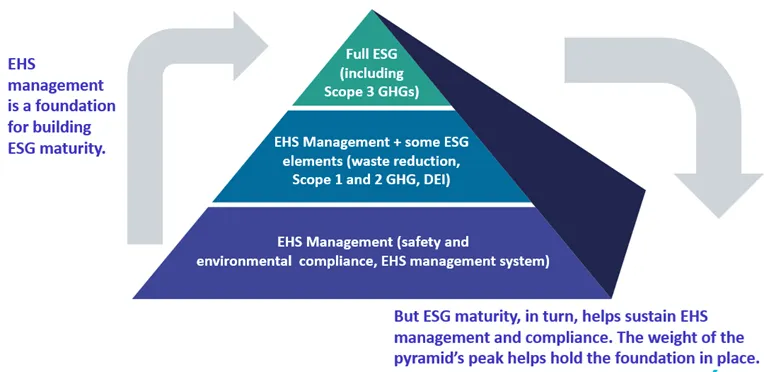
It’s this feat of connecting the peak of the pyramid to the foundation and expanding your current focus to include core EHS management tasks, that this article will be discussing.
Air Emissions
Let’s start off by looking at air emissions, because you probably already have at least a limited subset of these emissions on your radar. For example, you may have management of GHGs in your job description. You likely know about the three scopes of GHGs as defined by the GHG Protocol and have inventoried the GHGs associated with your company’s operations. For example, the GHG Protocol defines Scope 1 emissions as direct GHG emissions from your operations, Scope 2 emissions as emissions from generation of purchased electricity consumed by your company, and Scope 3 emissions as “indirect” emissions from sources influenced by your company’s operations, but not directly owned or operated by the company. Because so many organizations struggle with Scope 3 emissions, GHG Protocol also has a specific Corporate Value Chain (Scope 3) Standard that established industry-accepted accounting practices for Scope 3 emissions and defines 15 categories of Scope 3 emissions that are either upstream or downstream of your company’s operations.
All of that is essential information to help you succeed in your role. But you’ll still need to go deeper into your company’s air emissions profile. GHGs and other air pollutants, such as particulate matter (PM) and volatile organic compounds (VOCs), come from some of the same on-site processes, such as operation of air pollution control devices that combust fuel. But you also have many other air emissions sources from very specific processes for very specific contaminants. For example, if you are a wood furniture manufacturer, you likely have particulate emissions from sawing or cutting wood components, and VOCs and possibly hazardous air pollutants (HAP) emissions from flow coating of wood. All these emissions affect your regulatory compliance, the safety of your employees, and your impact on the environment and local communities.
Here again, it’s a good idea to have some conversations with your corporate EHS management. Find out if your site has air emissions permits, and review copies of them. Go out on the shop floor and review the processes that generate air emissions with department supervisors and front-line employees and take stock of your air pollution control equipment. You may want to talk to facilities management/maintenance staff to get some additional technical details, too.
As you assimilate this information, form a picture of how the chemical raw materials your company uses contribute to your air emissions profile. This will help you later to sharpen your focus on chemical management as the source of many of your current challenges, as well as an opportunity to improve your ESG performance.
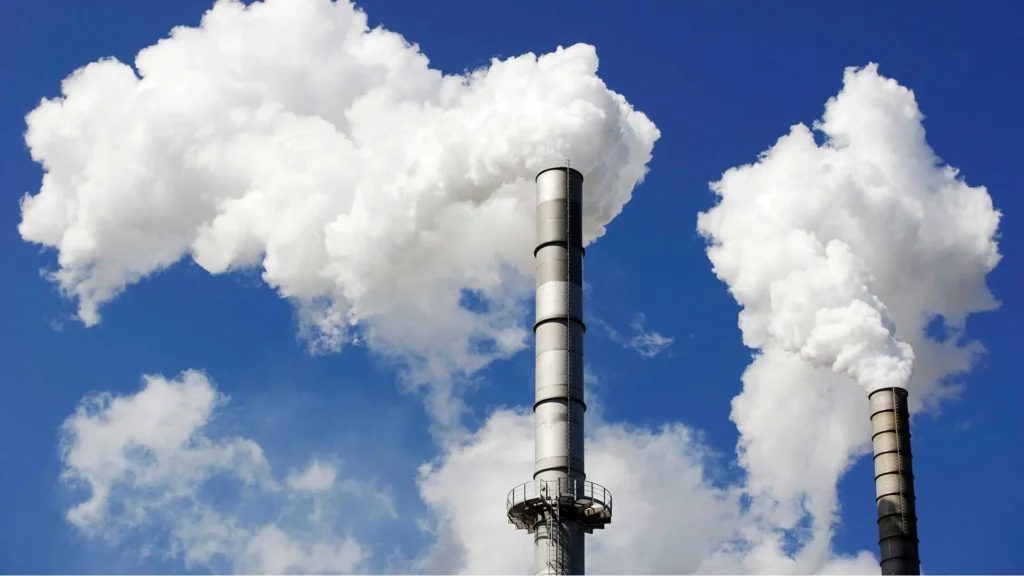
Another area of ESG you’re likely tasked with managing to some degree is energy usage. And here, it’s important to realize that understanding your energy consumption is inextricably tied to your ability to form an accurate picture of air emissions. If you have on-site fuel combustion sources such as process boilers, you’ll have associated emissions of air contaminants such as particulate matter (PM) and carbon dioxide (a GHG), as calculated using industry-accepted emissions factors. Depending on the types and scale of fuel combustion sources, the equipment may also be covered under an air emissions permit, which means you’d be required to calculate and report emissions.
And of course, you can only meet your responsibility to accurately report GHG emissions if you have accurate data regarding the utility-provided energy you consume, since the associated GHG emissions would be Scope 2 as defined by the GHG Protocol. Modern ESG software simplifies utility data collection by syncing directly with your utility provider, eliminating the need for time-intensive data entry and the potential for manual errors.
Waste Management
Waste management is one of the most common areas that company leadership will task a new ESG or sustainability manager with. You may envision your job involving management of company recycling programs – like printing out the signs indicating what kinds of materials employees can or cannot put into specific bins and training the maintenance staff on proper separation of recyclable materials and wastes sent to landfill. But these efforts, while important, are just the tip of the iceberg when it comes to sustainable waste management.
Expand your focus. You’ll need to develop a deeper understanding of all the waste your company generates, and more importantly, the processes and chemical choices that result in their generation. That means you’ll also need to understand more about what makes some waste more dangerous to human health and the environment than others. In the US, EPA calls those wastes hazardous wastes.
EPA regulates hazardous waste under the authority of the Resource Conservation and Recovery Act (RCRA). Under RCRA, EPA defines some chemicals as hazardous wastes through inclusion on specific lists (F, K,P, and U), and establishes criteria for other wastes to be classified as hazardous based on characteristics of corrosivity, ignitability, reactivity, and toxicity. For example, EPA defines a waste as corrosive if it has a pH of less than or equal to 2, or greater than or equal to 12.5. The pH of the chemicals you bring onsite as raw materials will be one of the biggest predictors of the pH of your waste, and whether those wastes will be corrosive hazardous wastes. This means that proper management of hazardous waste, including correct profiling of waste as hazardous or non-hazardous, starts with having an up-to-date library of all safety data sheets (SDSs), and easy access to information within the SDS, such as physical characteristics, including pH.
Let’s take it a step further. By reviewing SDSs and associated hazard information about chemicals before your company signs any purchase orders to bring the chemicals onsite, you can potentially make better choices, and reduce your hazardous waste generation right at the source. In the process, you’ll make your workplace safer because you’ll be bringing less dangerous chemicals into contact with your employees. And that’s not all. You’ll also improve your management of other areas of sustainability and ESG, including GHG emissions.
Here’s how that works. Let’s assume you’re not doing any on-site waste treatment, and like many companies, are sending your company’s waste to offsite treatment, storage, and disposal facilities (TSDFs). Your general, non-recycled waste will go to a landfill. Your hazardous wastes, on the other hand, will require special treatment at designated and licensed TSDFs, including fuel blending or incineration. The TSDFs will combust fuel during this treatment, which will result in emission of GHGs. And even though your company isn’t directly emitting these GHGs, your company does affect the level of GHGs at the TSDF by sending waste there for treatment.
In GHG accounting practices, these GHGs would be considered Scope 3 relative to your operation. Increasingly, stakeholders expect companies to track these “value chain” GHG emissions, and more importantly, to reduce their emissions. Modern green chemistry software helps you choose better chemical ingredients that don’t become hazardous wastes, thereby helping you reduce the amount of hazardous waste you send to TSDFs and associated Scope 3 emissions.
Chemical Management
So far, the aspects of EHS we’ve covered were probably on your radar somewhat, although possibly not to the same extent we’ve talked about them. But you might not have had chemical management on your radar yet at all, especially if you’re not coming into your role from an EHS background.
Yet, so much of your sustainability performance starts with better chemical management. Think about the areas of ESG we’ve reviewed so far: air emissions and waste management. The choices of chemicals you make affect those areas. Some of the chemicals in your inventory find their way into your air emissions, and even though we haven’t discussed it here, into your water discharges. If those chemicals are regulated pollutants, such as HAPs under EPA’s Clean Air Act (CAA) or priority pollutants under EPA’s Clean Water Act (CWA), they’re going to add to your company’s regulatory obligations. Additionally, as discussed above, some of your chemicals will become hazardous waste and pose significant risks to human health and the environment.
As a sustainability manager, you need to understand this to have the complete picture of your company’s environmental impacts and their root causes in your chemical inventory. So many of your responsibilities start with chemical management, as the image below shows. By using green chemistry software tools, you can assess the risks to human health and the environment of chemicals before you bring them onsite and choose safer and more sustainable alternatives. In doing so, you’ll set yourself up for success as an ESG and sustainability manager, because the impact of those better choices will reverberate throughout your supply chain. You’ll create less exposure risks for your workers, generate less hazardous waste, emit fewer air and water pollutants, and reduce chemical exposure hazards for communities and value chain partners.
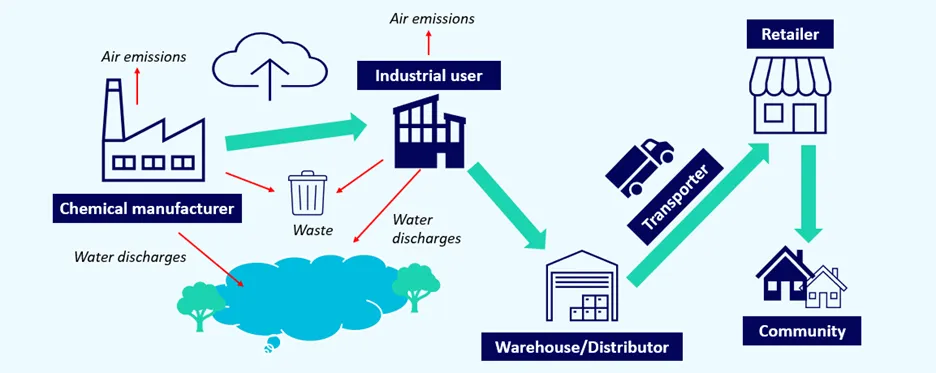
How Does the “S” in “ESG” Connect to EHS?
Depending on the scope of your role, it’s possible your job description includes managing Diversity, Equity and Inclusion (DEI) and internal sustainability initiatives, including protection of workplace psychological safety. You may not yet see the connections between these responsibilities and your company’s EHS management practices, but the connections may become clearer as we explore a bit further.
DEI is Connected to EHS
Many people might think of DEI as a largely Human Resources (HR)-led initiative, involving efforts to recruit and promote employees from historically excluded populations, and coordinating employee “affinity groups” to help representatives of these populations advocate for inclusive and equitable treatment. It’s been less common to see EHS managers directly involved in managing DEI programs, but that trend has been changing in recent years, with more webinars and conference talks on the connection between DEI and safety management.
At its foundation, DEI is not only about bringing people of diverse identities and backgrounds into the workplace but protecting their safety (in every sense of the word) and providing equal opportunities for success once they get there. To successfully meet DEI objectives, you must assess the differing safety needs and challenges across your workforce. For example, one historically significant problem has been that manufacturers of personal protective equipment (PPE) have often designed their equipment for average-sized male workers, leaving everyone outside of that physical size range, including most women, without adequate PPE. Employers themselves also designed workstations as “one size fits all” – accounting for the average size and strength of the typical (or often, typical male) worker and ignoring the diversity of ranges of size and strength in the workplace. Combined with the common lack of a systematic approach to ergonomics, many workers not only feel excluded from decisions affecting their safety but are at greater risk to their safety because of those exclusions.
Are there safety best practices that can help you improve your DEI initiative effectiveness in the ways that matter most, while also addressing occupational safety risks? Absolutely. At a “meta” level, it starts with improving participation in your safety program. Here are some specific things you can start doing now to get the level of engagement you need:
Talk to the right people. Do you have the right people involved in your safety program? Chances are, there are some employees who have important expertise in specific aspects of your operations and their associated risks that you‘re not hearing from yet, but should be. Start having additional conversations with employees, supervisors and EHS managers, and listening for details about employees in specific departments or in job roles that seem like they’d add something to your program. Then, reach out to those employees and start building relationships. Include them in safety team meetings, and when necessary, set up some one-on-one time with them to learn more about their role, and how you can support them. You’ll be fostering inclusion, while also learning what you need to learn to manage safety more effectively.
Facilitate employee participation in safety management. The natural follow-up after you’ve identified employees to actively include in your safety program is to make it easy for them to participate. The conversations you have with your safety team members will help you identify areas for improvement. For example, a common failing is that the incident management process is too time-consuming or has too many barriers to initiate an incident report, which de-incentivizes reporting. The right safety management software can help here, by enabling you and your employees to perform key safety tasks such as inspections and incident investigations from anywhere, so your whole workforce can play a direct role in safety management.
Focus on ergonomics. You may not hear about the connection between ergonomics and DEI as much as you should, but the two fit naturally together. That’s because ergonomics is the process of fitting the work environment to the worker – systematically identifying and controlling potential for musculoskeletal disorders (MSDs), which are injuries to muscles, tendons, ligaments, joints, and nerves from overexertion, repetitive motions, or awkward motions. This focus on the worker is an important part of recognizing the diversity of physical size and physical ability of populations of employees in your workplace, and making sure your safety programs are accounting for that diversity.
The best modern ergonomics solutions make this easy to do, with machine learning (ML) capabilities that capture employee physical motion while they’re performing job tasks, and then provide expert-curated root cause assessments for associated MSD risks and help identify corrective actions. Best of all, employees will see how the ergonomics software helps protect their safety and be able to directly participate in the assessment process, and in identification of follow-up actions, which will further their sense of belonging.
Protecting Psychological Safety
As an ESG or sustainability manager, you’ve probably already encountered the term psychological safety, but may not understand exactly what it means. One way to think of psychological safety may be in terms of an absence of psychologically unsafe conditions. The common term for those conditions is psychosocial risks, which refers to sources of anxiety in the workplace rooted in the nature of the work itself, such as the structuring of work shifts, the physical design of the workstation, or the presence of environmental hazards such as heat or chemical exposures. If employees know there are unaddressed or uncontrolled hazards in their workplace, this creates anxiety for them which itself poses additional direct and indirect risks, as shown in the diagram below, adapted from the World Health Organization (WHO) guide Health Impact of Psychosocial Hazards at Work: An Overview.
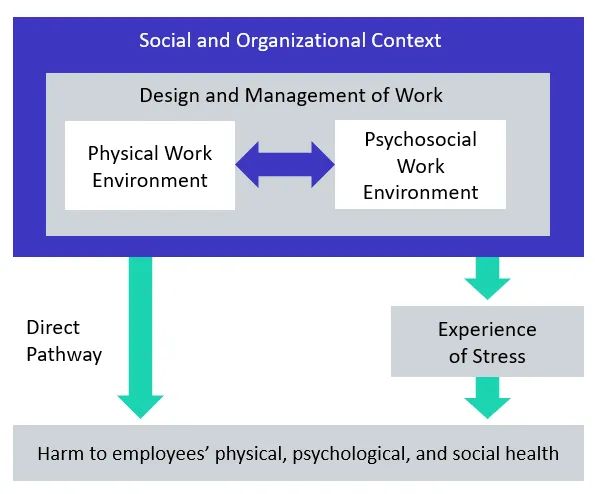
Direct risks include stress and increased potential for related illnesses such as hypertension and heart disease. Indirect risks include the possibility for stress to distract worker’s attention while working and sustain injuries, or for tightening of muscles as a physiological result of stress to increase risks of musculoskeletal disorders (MSDs).
But there’s another, more positive way that you can frame psychological safety. Rather than just viewing it as the lack of something bad, you can frame it as the presence of something good. Namely, you want to build a workplace safety culture that promotes employee engagement, and makes everyone in your workplace feel they belong, and that their contributions matter. But again, you can only succeed if you first get a good handle on occupational safety and health.
You’ll need to get into the weeds, build relationships with EHS managers, and get out on the shop floor to talk to employees. Understand what’s working, and where your challenges are today. It may be that you have a difficult, time-intensive method for reporting safety incidents and observations, which is preventing progress on addressing risks (both physical and psychological) and leading to employee disillusionment with your safety program. Or, perhaps you’re struggling with follow-up actions from incidents, whether it’s to effectively complete them, or to have easy ways to generate reports on actions to share progress with employees. Modern safety management software makes it easier to involve employees in the process of developing actions that work, and generating reports showing that actions are addressed. This, in turn, not only reduces employee anxiety but also makes employees more likely to participate in your safety program in the future.
Better Data to Drive Better ESG Performance
We’ve covered a lot of ground in this piece. Let’s bring things back to one of your core responsibilities as an ESG or sustainability manager: managing data and ESG disclosures.
The term investment grade data is now part of the ESG lexicon, used to refer to ESG data that is timely, accurate, complete, and auditable. As the term implies, this is the kind of data that is most useful to the investment community, to help identify risks and aspects of business performance not captured by traditional financial reporting. Investors using the data need to have confidence that it’s accurate and reliable as a potential source for decision making. As an ESG and sustainability manager, you’ll have a role to play in ensuring your company’s ESG data meets these stringent criteria.
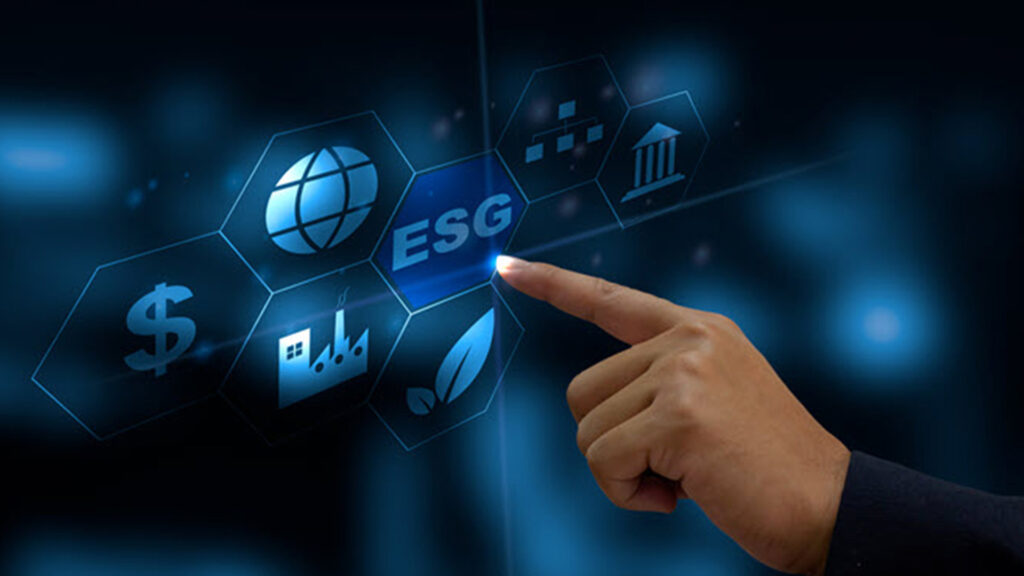
How do you accomplish that? First, keep in mind everything we’ve discussed to this point, and realize that your ability to understand and manage your data depends on understanding key aspects of EHS management, including air, water, and waste. And second, understand that you’re very unlikely to consistently collect good data and generate good reports if you’re still dependent on manual data management processes.
Think about the work involved in gathering energy data manually. Chances are, you don’t need to think very hard to imagine it, because you’re currently doing it that way. You have to chase down utility bills from your providers, and physically type the data into a spreadsheet or tracking software, which introduces the potential for manual entry errors, especially if you need to do this multiple times for different facilities under your responsibility. And because utility providers won’t always provide data in the units that you and your company need them in for your official reporting, you’ll probably need to do some unit conversion calculations, which represents more potential for error. And finally, to determine emissions of specific air pollutants associated with energy combustion, you’ll need to find and apply the correct emissions factors, and there’s plenty of possibility for error there, too.
We alluded earlier to the time-savings possible with utility data integration capabilities, but the even bigger benefit may be with data integrity. The best modern ESG software directly interfaces with your utility company to collect electronic copies of your bills, extract your usage data, and automatically convert it into the units you need. The software also applies the correct emission factors, giving your accurate emissions based on combustion.
Looking for More Information?
As we noted toward the beginning of this article, you probably already know that ESG and sustainability are important, because they’re part of your job title. But hopefully, through our discussion, you now have an even deeper appreciation for the importance of ESG, and how your ESG maturity builds upon and depends upon excellent EHS management practices.
We hope you’ll continue building upon your knowledge base and establish good relationships with EHS personnel and all employees involved in your EHS management system. And if you’re looking for more information in the meantime, we’ve got you covered.
Our eBook “ISO 14001: Using the Standard to Improve Environmental Management” will help you better understand how your sustainability work builds upon EHS management.
For more information about how better chemical choices will improve many aspects of ESG management, check out our on-demand webinar Using Chemical Management & Green Chemistry to Improve Your ESG Maturity & Value Chain Relationships.
And as always, be sure to follow us on LinkedIn for the latest updates on EHS and ESG.
Let VelocityEHS Help!
We’ve built our entire VelocityEHS Accelerate® Platform to help EHS professionals like you become safer and more sustainable. Our Safety Solution helps streamline your most important safety management tasks, like incident management, inspections, follow-up actions, and maintaining and providing access to SDSs. Our Green Chemistry solution builds on that by facilitating smarter choices of chemicals that pose fewer risks to your employees, communities and the environment and lighten your compliance burden. And our Environmental Compliance solution can help you streamline management of air and water discharges and waste shipments and easily complete your TRI/Form R reporting.
Using our Ergonomics solution, you can move from a reactive to proactive safety management approach using AI tools to not only assess MSD risks using a mobile phone, but more importantly, provide actionable, expert-curated insights to help you identify root causes and corrective actions.
Our ESG Software provides exactly the support you need to track all three scopes of your GHG emissions, with reporting capabilities aligned with major ESG disclosure frameworks. The Utility Data Sync capability within the software even automatically collects your energy usage data directly from your utility provider, apply the correct emission factors and convert data to the units you need – minimizing potential for error and administrative burdens. Materiality assessment capabilities within the software also help you easily generate surveys you can share with stakeholders, including members of your EHS management team you’ll need to work with to achieve your goals.
Request a demo or contact us today to learn more about how we can support your continuing ESG journey.