Manual material handling (MMH) is one of the most prevalent types of work performed across industries. It involves the spatial manipulation of objects (raw materials, product, etc.) and is a basic form of work that requires minimal qualifications or experience.
MMH Tasks Expose Workers to All Primary MSD Risk Factors
MMH requires the body to move in the most complex ways, and it consistently subjects workers to bending, twisting, reaching, lifting, pushing, and pulling, among a multitude of other physical demands. MMH usually involves exposure to all primary risk factors that cause musculoskeletal disorders (MSDs), such as force, posture, duration, and frequency, which can affect all regions of the body. The trunk of the body, however, is the physical center point exposed to the most stress. In 2020, there were 301,890 musculoskeletal disorders reported to the U.S. Bureau of Labor Statistics, 46% of them to the trunk and 37% specific to the back.
The short and long-term implications of such injuries are detrimental to workers and organizations as a whole. The overall cost to workers and organizations is both quantitative and qualitative, and it totals to a substantial one:
- Quality-of-life years lost
- Forced retirement
- Opioid addiction and deaths
- Medical bills
- Loss in productivity, quality, and workdays
- Workers’ compensation complications
To name a few. Workplace injuries have visible costs that seem obvious, but they have many more hidden costs that may not be seen immediately after an incident occurs—much like how an iceberg’s mass lies below the water’s surface, out of eyesight.
Is MSD Risk in Manual Material Handling Tasks Unavoidable?
MMH is a necessary aspect of most operations, but that doesn’t mean that these injuries are unavoidable. MSD risk levels for employees can be identified by using ergonomics assessment tools and reduced by implementing improvements that mitigate current and future risks.
In many instances, reducing risk to the back or trunk will also reduce the risk to other involved body regions. For example, if a worker lifts a 30 lb. box off of the ground and carries that box 15 ft. to a workbench, there will be risk to the trunk from bending and lifting the box; the upper limbs from reaching for the box and lifting it; the lower limbs from kneeling and lifting; and the neck, from the strain of operators often extending their head to keep a level line of sight when grabbing the box.
How to Reduce MSD Risk in Manual Material Handling Tasks
Paired with proper coaching, a height-adjustable lift cart could remove almost all of the risk exposure to the back, in this situation, by staging the box on the lift cart instead of the ground. The operator could use the cart to transport the box to the workbench, and then elevate the box using the cart controls to slide the box instead of lifting it. By removing the need to bend over (posture), lift and carry (force), risk of force and awkward postures to all other body regions involved with the task would also be reduced.
There are a few fundamental, high-impact improvements that safety teams can make to their MMH operations to reduce risk as described above. Implementing the following controls prior to new MMH operations, or injecting them into pre-existing operations, can address a substantial amount of MSD risk that is otherwise guaranteed in most situations.
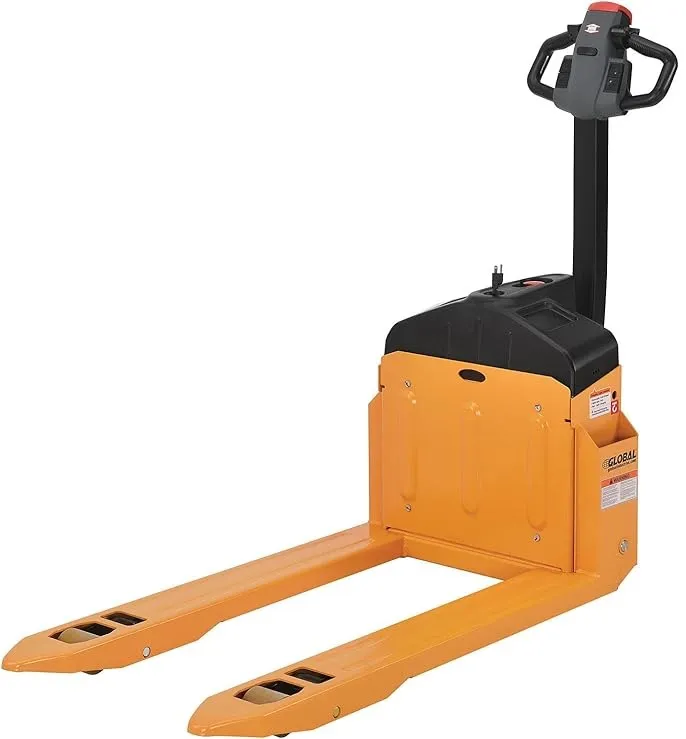
Motorized Pallet Jacks
Pallet jacks are devices that are designed to lift and transport pallets. Manual pallet jacks enable a single operator to perform this task by pumping a handle to lift the load and pushing or pulling the pallet to maneuver. Both adjustment activities can expose operators to frequent and prolonged excessive forces and awkward postures.
- Motorized pallet jacks automatically raise the pallet and enable the operator to transport and position the load with little to no force.
- Utilize a 2-handed push-handle design to help mitigate risk for both force and posture, as a 1-handed pull design will still expose operators to awkward postures.
Height-Adjustable Carts
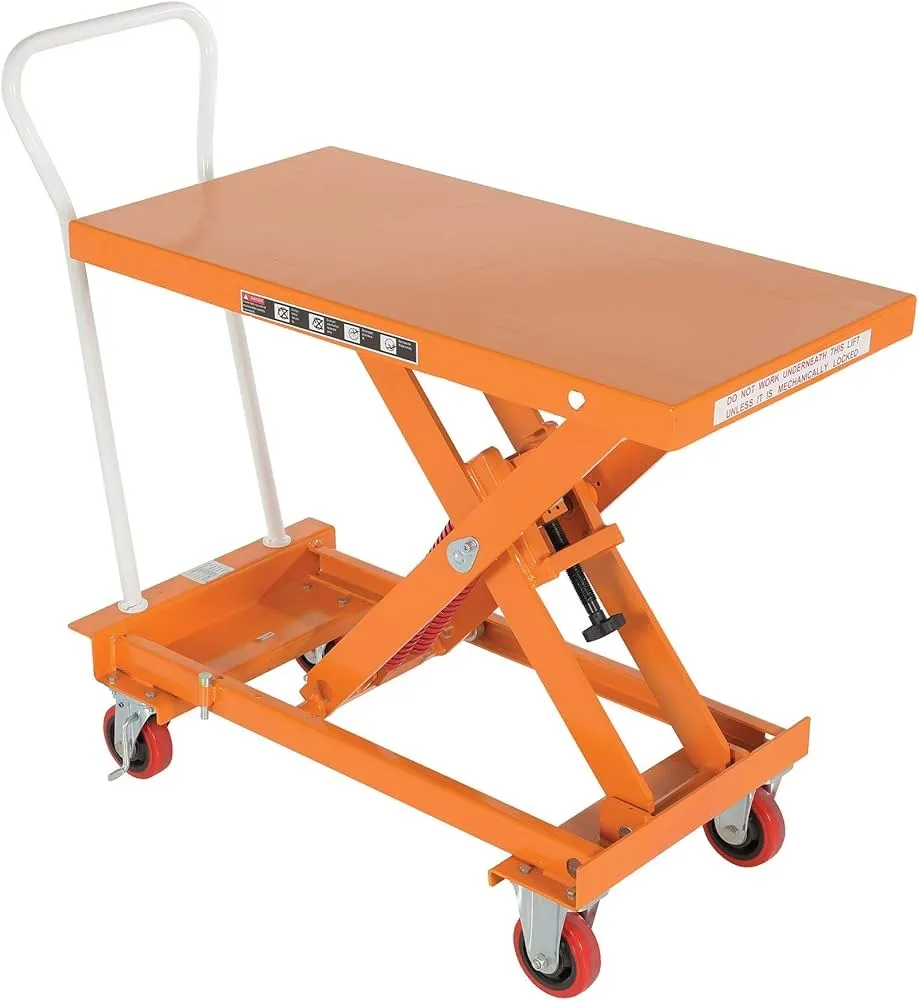
Carts are available with flat surfaces, bins, or shelves and are used to transport materials by pushing or pulling. They can remove the need to carry an item between two points and can be used as a staging surface. If the height of a cart surface is level with the target surface, it replaces the need to lift/lower an object with the ability to horizontally slide the object.
A cart without height adjustability will still expose operators to all risks
involved with lifting or lowering when objects need to be moved from the cart to the staging surface.
- Height adjustable carts are one of the highest-impact, lowest-cost improvements that can be made in many manual material handling operations.
- In a recent systematic review, height-adjustable carts were shown to significantly reduce risk of injury compared to traditional carts.
- Manual or motor actuated carts are available, and the motorized versions remove the need to manually pump or crank the cart.
- Because manual adjustment mechanisms can be cumbersome and time consuming to use, they can act as a deterrent to proper use and should therefore be selected only if motorized versions are not available.
Lift Tables
Height adjustable lift tables enable the vertical positioning of materials. By staging a pallet on a lift table, as opposed to a non-adjustable staging surface, materials can be placed at optimal hand working heights for operators through all levels of a pallet. There are several options for these devices:
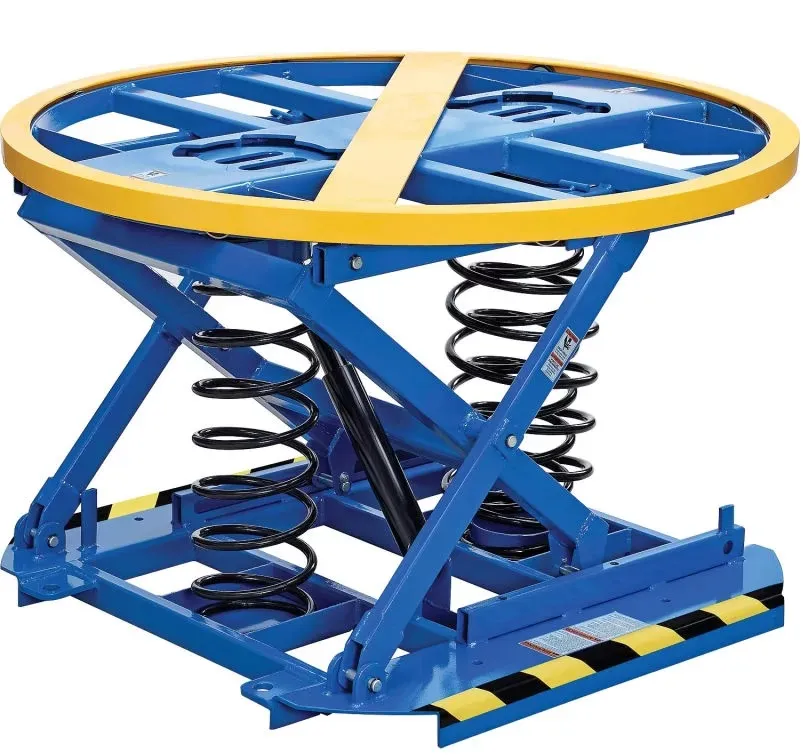
Self-leveling lift tables are those which automatically increase or decrease in height as the weight on the lift table varies. For instance, a full pallet that is 60″ tall will cause the lift table to lower itself to the ground. The table will then increase in height as items are removed from the pallet. If the lift table is calibrated to the correct weight, it will remain lowered until operators reach optimum hand-working height. Then, with each item removed, the table will elevate to maintain optimum hand-working height for operators until the final layer of the pallet is unloaded. Some lift tables automatically rotate the pallet so that objects on all sides of the pallet can be retrieved by the operator without excessive reaching.
- Spring loaded lift tables rely on a spring mechanism to actuate vertical movement and rotational movement. While they are dependable, they require a minimum weight and may not be suitable for exceptionally light weight pallets.
- Airbag lift tables serve the same purpose as spring loaded and can be used for lighter pallets. They are also dependable, but they require routine pressurization for ongoing use.
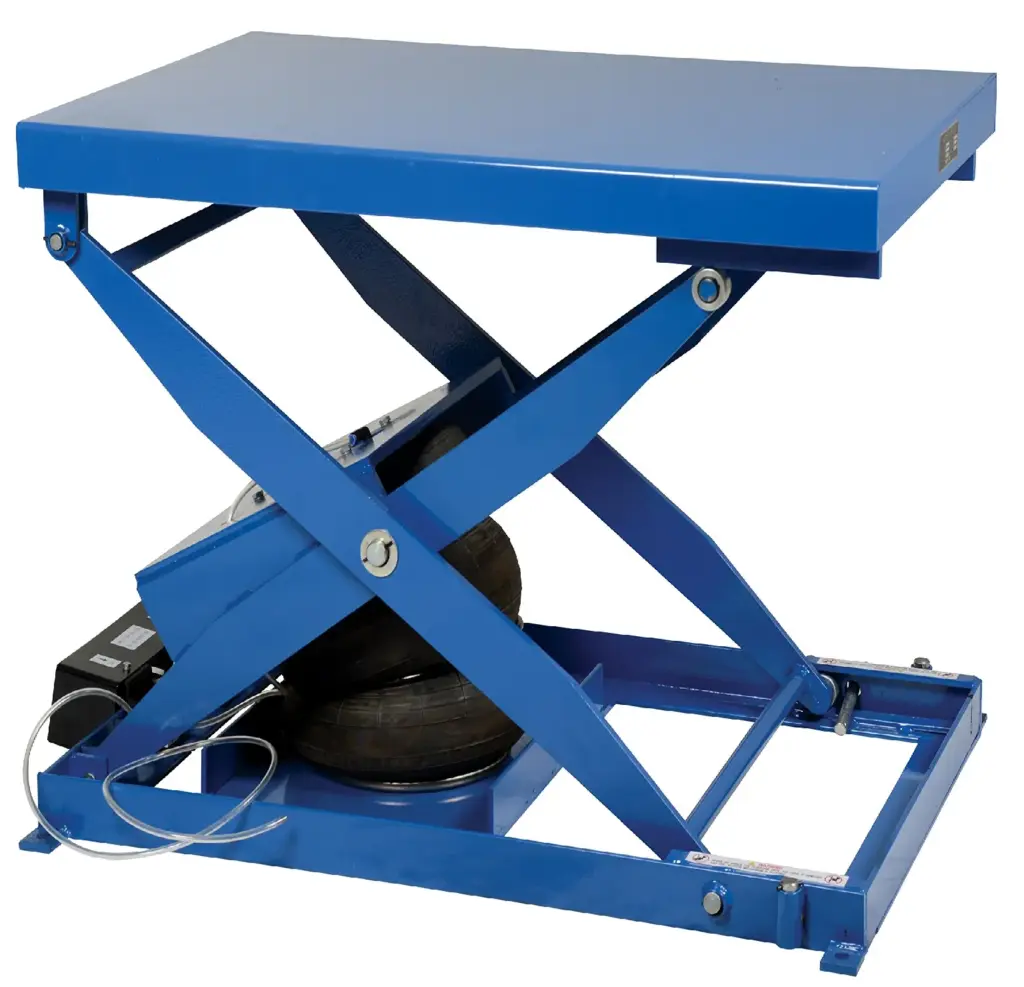
Manually adjustable lift tables require cranking or pumping to set the height and come with similar complications as the manually adjustable carts described above. These types of lift tables tend to be the least utilized by operators, as manual adjustment is time consuming and sometimes counterintuitive to a goal.
Motorized lift tables are actuated mechanically or hydraulically and enable the vertical positioning of loads using a hand control. They are dependable but require more maintenance than non-motorized versions and ultimately cost more. Properly coaching operators on positioning for optimal hand working height is necessary. Another option is to control the vertical adjustment with a switch, activated by a weight or light sensor.
Coaching
Coaching is a method that, when used in place of engineering controls, is ineffective. When used in conjunction with engineering controls, however, coaching enhances the impact of those controls.
- Be sure to provide coaching on proper use of equipment to ensure that operators know how to utilize the equipment as intended.
- Doing so will ensure that the project risk reduction is reflected in the follow-up assessment
By identifying the risk factors of manual material handling tasks through ergonomics assessments and then implementing effective controls to address those risks, MMH tasks don’t have to put employees at risk for developing MSDs.
Sources
- Christoph H. Glock, Eric H. Grosse, W. Patrick Neumann & Andrew Feldman (2020): Assistive devices for manual materials handling in warehouses: a systematic literature review, International Journal of Production Research, DOI: 10.1080/00207543.2020.1853845
- McGowan, Blake (2020): Opioid-Related Overdose Deaths Are Still Devastating Communities; Here’s How Ergonomics Can Help. Risk & Insurance, https://riskandinsurance.com/opioid-related-overdose-deaths-are-still-devastating-communities-heres-how-ergonomics-can-help/
- U.S. Bureau of Labor Statistics – https://www.bls.gov/