It’s a common practice for companies to use contractors or temporary workers to complete projects, with some companies even having a constant stream of temporary workers coming on site. A 2020 Career Builder study found that the majority of employers in some industries, such as information technology and manufacturing, planned to hire temporary workers—75% and 59%, respectively. Additionally, these companies often have visitors on the premises. This creates unique safety challenges and potential liabilities that businesses must be aware of and properly address as they work toward achieving or maintaining EHS and ESG maturity.
Managing contractors, temporary workers and visitors, making sure they’ve completed the necessary training, and ensuring they have the proper credentials and permits can be a daunting task. An effective control of work (CoW) management system is essential for mitigating risk and ensuring safety.
What Exactly is Control of Work?
Control of work is an element of risk management that keeps everyone in a work environment safe by ensuring that contractors, temporary workers and visitors have the proper training, credentials and/or worker permits to be on site. It’s an essential element of a comprehensive EHS program and acts as a gate for the workplace.
Control of work management systems also support effective application of the contractor safety management lifecycle (below), which provides a formal framework for planning, evaluation and selection, implementation, onboarding/induction, and safety performance review of contractors and temporary workers.
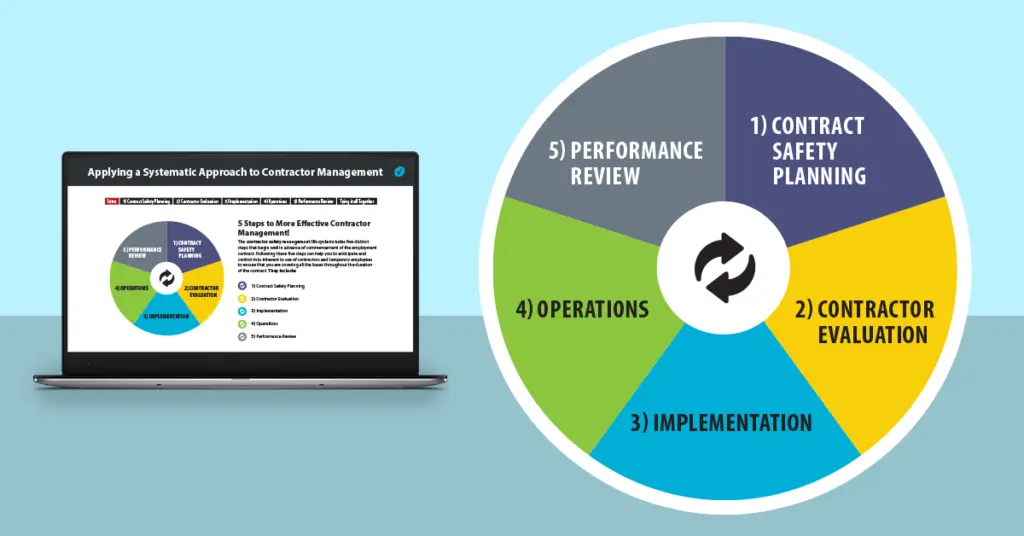
The contractor safety management lifecycle blends control of work processes with continuous improvement principles so that data, best practices, and lessons learned can be integrated throughout the system.
Control of work is a critical component of managing operational risk at every level of the organization. It ensures that hazardous tasks to be performed by a contractor or temporary worker, such as confined space entry or hot work like welding and brazing, don’t take place until all work permits and verifications have been met.
Simply put, control of work is a seamless system to manage a contractor or visitor’s journey from start to finish across work locations.
Why Control of Work Is So Important
Numerous studies show that contractors and temporary workers are at elevated risk for workplace injury and illness. An analysis performed by researchers at ProPublica.org found that the incidence of workplace injuries for temporary workers was between 36-72% higher than that for full-time regular employees. Another study conducted by the National Council for Occupational Safety & Health (NCOSH) showed that temporary workers, who represent just 2% of the U.S. workforce, accounted for 17% of work-related fatalities.
This is especially noteworthy for industries that heavily rely on temporary workers. In manufacturing, for example, temporary employment continues to significantly outpace the average utilization rate compared to other industries. A 2018 BLS report analyzed data from the US Census Bureau’s Current Population Survey (CPS) and the US Department of Labor’s Occupational Employment Statistics Survey (OES) and revealed that since the Great Recession (2008-2017), manufacturing utilization of temporary workers ranged between 5.2% and 10.3%, whereas the overall average for all industries during that same period was around 2%.
The findings of these studies and others like them suggest an inconvenient truth for employers—bringing temporary workers or contractors into the workplace is likely to introduce additional EHS risks to the organization and its employees. While temporary labor can provide financial and operational advantages compared to full-time permanent employees, those benefits can be quickly erased by overwhelming financial liabilities and damage if the safety of temporary workers is poorly managed.
When it comes to managing the safety of temporary labor, the first step is understanding the root causes of why these injuries and illnesses occur at a higher rate. Employers generally possess less control over the performance of temporary workers and contractors than over their own employees when it comes to workplace safety.
Contributing factors of this could be poor communication of training and hazard information, confusion between temporary workers and the employer regarding obligations, qualifications of the temporary workers not being properly vetted and approved, or not having the proper worker permits established.
Therefore, employers should strive to provide added layers of protection when temporary workers and contractors are on-site. That way, they can ensure that all work is being performed in accordance with their own high safety performance standards, and they are doing all they can to protect temporary workers. That’s where the value of a formal control of work management system really comes into play.
The Value of Control of Work
As mentioned earlier, control of work management systems provides manufacturers with a highly visible and traceable means of verifying that contractors and temporary workers possess the necessary skills, training, and hazard controls to perform jobs safely. An important and often requisite component to control of work to ensure contractor and temporary workers safety is the implementation and maintenance of a permit-to-work system. It can be helpful to think of PTW as a sub-system that provides an added layer of protection within a control of work management system.
Control of work and permit to work systems also provide assurance that temporary workers like contractor providers and staffing agencies meet all requirements with respect to regulatory compliance, safety performance, liability coverage, or any other qualifications and criteria set forth. From an administrative standpoint, they also provide enhanced visibility of work activities across multiple facilities and inform more detailed safe work plans (SWPs) that effectively address the hazards that may be introduced due to the presence and activities of contract and temporary workers.
The ability to monitor what jobs are being performed, when and where they are being performed, and who is performing them is also a valuable advantage for departments outside of EHS. HR, facility security, maintenance, operations, payroll, and many other teams benefit from the ability to schedule, coordinate, and monitor the presence of temporary workers, contractors, and visitors on-site.
Finally, formal control of work and permit to work systems provide an effective communication framework that promotes collaboration and coordination between employers and temporary workers. This makes it easier to ensure all parties to the employment contract are aware of their obligations for contractor and temporary worker safety, and verify that all necessary training, hazard controls, personal protective equipment (PPE) and other job-specific precautions are in place prior to work. This understanding and communication is a crucial, yet often an overlooked component of contractor and temporary worker safety, which has been shown to be a significant factor in injury and illness prevention.
A Software Solution to Ease the Control of Work Burden
With permit-to-work, contractor management, visitor management, and additional control of work tools, the VelocityEHS Contractor Safety & Permit to Work Solution can ensure temporary workers and contractors have been properly vetted, trained, and approved. VelocityEHS Contractor Safety & Permit to Work helps manufacturers and employers across all industries seamlessly manage complete contractor journeys and electronic permit-to-work processes across locations through a single centralized system.