By Greg Duncan, MELP, CSP, Sr. EHS & ESG Content Manager at VelocityEHS
One of the most important steps in performing any job safety analysis (JSA) is assessing the likelihood and severity of risks encountered during performance of job tasks. This risk assessment is crucial to the subsequent JSA steps of identifying and implementing the appropriate hazard controls, as well as evaluating the effectiveness of those controls to verify that risks are managed to an acceptable level. One of the greatest challenges with JSA risk assessment, however, is that different people with a diverse range of knowledge, skills, expertise, and perspectives who are performing the JSA can unfortunately introduce discrepancies in how risks are perceived and evaluated. These discrepancies can result in uncontrolled risks to workers, poorly designed or ineffective hazard controls, and ultimately, an unsafe workplace.
To help illustrate this challenge, let’s look at a risk matrix. EHS professionals are likely familiar with the concept of a risk matrix which commonly uses qualitative terms like high/medium/low to describe and evaluate risk severity, likelihood, and overall risk level.

A risk matrix is certainly a valuable tool for documenting JSA risk assessment and communicating those risks in an easy to understand format, but it has its limitations. Specifically, a risk matrix that relies on qualitative risk assessment criteria (high/medium/low) to evaluate the likelihood and severity of risks fails to give us a precise picture of the actual risk level. To counter this, JSAs often incorporate additional risk factors such as the frequency of hazard exposures and number of workers exposed to help further assess the likelihood and severity of risks, but if we rely on qualitative terms to describe those additional risk factors as well, the JSA risk assessment is still imprecise .
This is because qualitative terms are inherently subjective, and how these terms are interpreted is heavily influenced by the risk perception of both the person(s) assessing the risk and the workers who rely on the JSA to inform safe work practices. A risk that is defined as “medium” in the JSA may be interpreted differently by different people, and therefore, the level of precaution and hazard controls workers employ when performing job tasks can vary significantly. This is a bad situation.
This lack of standardization can also lead to a situation where the risks documented in the JSAs for the same job performed in different areas of the workplace or across multiple locations are not assessed consistently. This can lead to different hazard controls being implemented to manage identical risks, and potentially, reliance on less-than-effective hazard controls. Moreover, it prevents any meaningful “apples-to-apples” comparison of incidents or other risk information concerning those jobs when evaluating job safety and/or periodically reviewing the JSA.
So, how can we standardize our risk assessment criteria so we can minimize the subjectivity in our JSAs and manage risks more consistently across the organization as a whole?
JSA Risk Assessment Best Practices
Standardize Your Safety Training
One of the fundamental goals of workplace safety training is ensuring workers possess the knowledge and skills necessary to recognize and avoid hazards, which should of course include the ability to accurately assess the likelihood and severity of those hazards. If you can develop and deliver safety training in a uniform manner to all workers performing the same jobs and even similar job tasks throughout the workplace (and across the entire organization), you’ll make significant progress toward standardizing and aligning workers’ perceptions of the hazards and risks associated with those job tasks. With a more uniform perception of job task hazards and risks, you’ll help to minimize the subjectivity in workers’ interpretation of job task risks so that all workers have a common understanding of how to recognize and control them.
This is, itself, a big challenge because there are a lot of variables that impact the effectiveness of workplace safety training. Different trainers, different training methods and content, trainees’ own attitudes and existing levels of knowledge and experience — these all influence how training is received and retained. If we, as safety professionals and trainers, can standardize not only what training we deliver but also how we train, then we give ourselves the best odds of giving workers the most comprehensive and accurate understanding of job task hazards and risks.
Hands-on learning will always be an essential aspect of workplace safety training, but eLearning (online computer-based training) helps to minimize the inherent variability in workplace training that can be introduced due to different trainers, training content, and training settings. It enables safety professionals to provide consistent, standardized training to workers and evaluate training performance and retention using a single, uniform set of metrics. This lends itself to a more consistent perception of job task hazards and risks among workers, and fosters a more uniform approach to controlling those risks using the most effective and accepted control measures.
Leverage the Knowledge & Experience of your JSA Team
There’s a reason I’ve addressed training as the first area of best practice here, and that’s because knowledge of hazard recognition and controls forms the foundation for the entire JSA process. If the people performing the JSA lack the ability to recognize job task hazards, consistently assess risks, and select the most appropriate and effective controls, the resulting JSA will be inadequate and incomplete, potentially leading to unrecognized and uncontrolled hazards.
That said, JSA should be a collaborative exercise that incorporates the knowledge of hazard recognition and control from multiple individuals. Two heads are better than one, right? How about three, or six, each bringing unique expertise and representing a diverse range of stakeholder interests. Performing JSA in a team setting allows for JSA team members to confer and ideally reach a consensus on how to properly evaluate and describe risks. This helps you to reduce the subjectivity of risk categorization and gain a more balanced and accurate assessment of risk likelihood and severity.
By performing JSA in a team setting, you’re simultaneously turning the whole exercise into a training opportunity with JSA team members actively learning from one another and developing a more consistent perception of risk. This further reduces the subjectivity of risk categorization and assessment. You might think that having a team of diverse voices and perspectives could complicate or confuse the JSA process, but when JSA is performed in a team setting, team members tend to develop a genuine sense of shared responsibility and accountability for workplace safety. This is particularly true when employees who perform the job being analyzed are included in the JSA team. When those workers are given a direct role in evaluating the risks they encounter on a day-to-day basis and in developing safe work practices and controls, this strengthens ownership, engagement, and understanding of job task safety. This has the direct benefit of improving the JSA, and the secondary benefit of fostering a more proactive safety culture within the organization.
Achieving the benefits of a team-based, collaborative JSA process is only possible, though, if you have JSA tools and systems that accommodate that collaborative approach. It’s difficult to coordinate and capture JSAs using a paper-based document, and paper-based JSA processes are severely limited in the ability to access, share, edit, update, and communicate JSA information. Unfortunately, many EHS professionals still rely on paper-based JSAs, and these limitations create barriers that keep them from realizing the full safety program benefits they are intended to provide. As a result, paper-based JSAs are often simply filed away, underutilized, infrequently updated, and only re-visited when something goes wrong.
Software-based JSA, by contrast, offers not only enhanced collaboration, access, updating and sharing capabilities, but system configuration options that allow JSA team members to quickly select from a centralized knowledge base of standard hazard definitions, risk assessment criteria, and hazard controls. This makes it easier to perform JSAs consistently and accurately from job to job and throughout your entire organization, further reducing the subjectivity when performing JSA risk assessment.
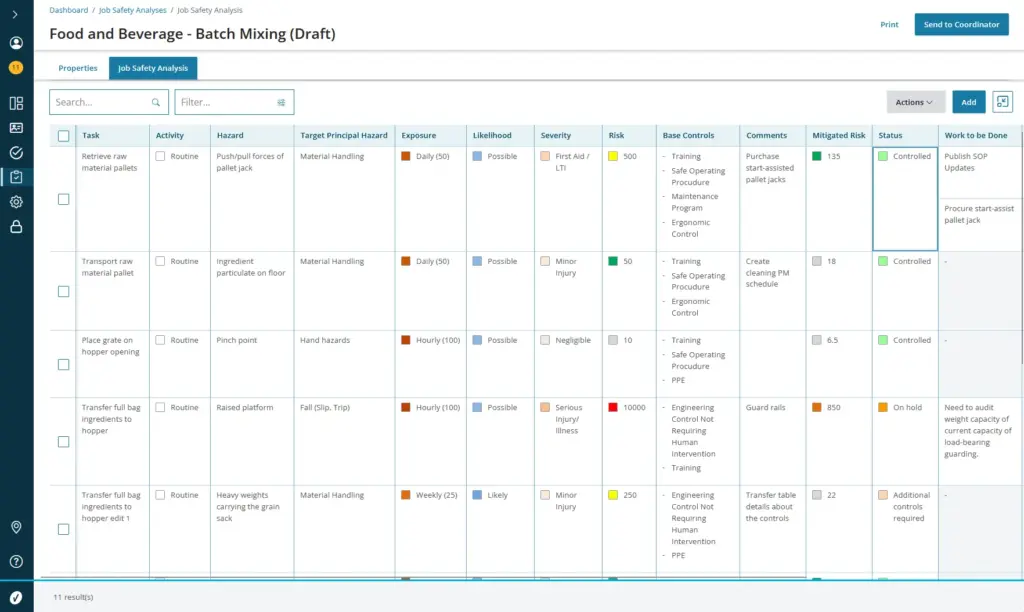
Incorporate Semi-Quantitative & Quantitative Risk Assessment Criteria in your JSAs
As we’ve already discussed, many EHS professionals rely on qualitative terms (high/medium/low) to describe risks when performing JSA risk assessment, and often depend solely on their best professional judgment to determine risk likelihood and severity. Relying purely on qualitative risk assessment criteria for risk likelihood and severity limits the accuracy of the JSA, even with the combined best professional judgement of the entire JSA team. This judgement and experience are certainly essential factors in assessing risks, but they fail to tell the whole story.
To minimize any confusion, EHS professionals should consider how to incorporate more quantitative risk assessment criteria into their JSAs to generate a semi-quantitative risk assessment. A go-to source for quantitative data to support more objective and standardized JSA risk assessment is your actual injury and illness records. Specifically, injuries and illnesses associated with the job being analyzed in the JSA. EHS professionals should ideally have injury and illness data in-hand when performing JSAs to support and confirm the judgement of the JSA team, providing empirical evidence of risk likelihood and severity.
Referencing historical incident data will help you to improve the accuracy of your JSA risk assessments while further minimizing the subjectivity of your risk assessment criteria. There are several common incident metrics you should consider when it comes to evaluating risk likelihood and severity for a given job. These include, but are not limited to:
Frequency metrics
- total recordable incident rate (TRIR)
- length/duration of hazard exposures
- lost time injury frequency rate (LTIFR)
- fatal accident rate (FAR)
- equipment failure rates/service life estimates
Impact metrics
- nature of injuries or illnesses (e.g. fatal vs. non-fatal injuries, extent of injuries)days away restricted or transferred (DART) and other commonly tracked incident rates)
- number of workers affected/involved
- direct costs of injuries and illnesses (medical treatment, workers’ compensation claims, legal penalties, etc.)
- indirect costs (civil liability, lost productivity/downtime, worker turnover and retraining, reputational damage, etc.)
Earlier on, we mentioned incorporating frequency of hazard exposures and number of workers exposed as additional criteria that can help us better assess the likelihood and severity of risks. Incorporating these criteria not only gives a more defined picture of risk, but describing these additional criteria quantitatively or even semi-quantitatively (see below) will further minimize the subjectivity of our JSA risk assessments and standardize our perception of risk likelihood and severity.
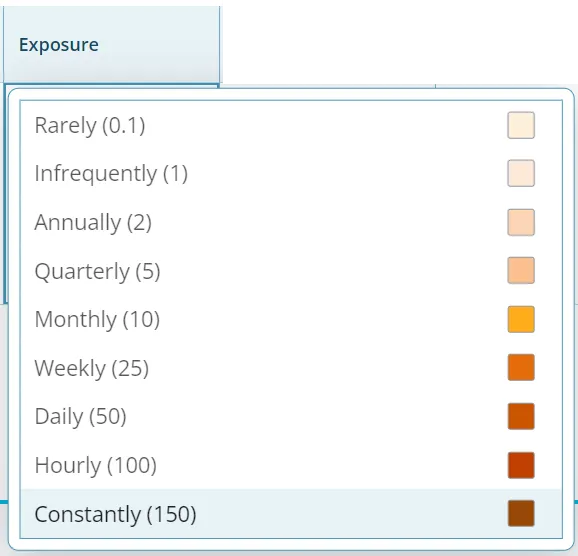
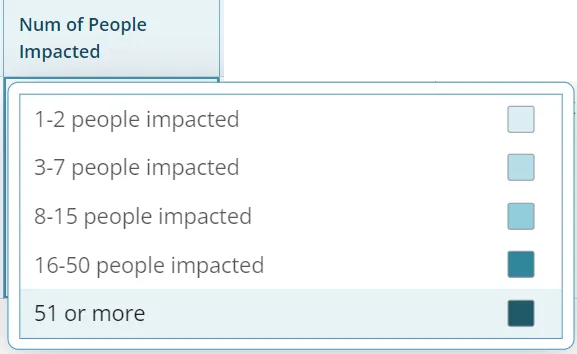
Applying more qualitative criteria to your JSA risk assessment will help you generate a more objective, standardized picture of workplace risks, but it first requires tracking this data and being able to easily reference it when performing JSA. This way, you’ll be able to access, calculate, compare, and apply this information easily when performing your JSA risk assessments so you don’t have to hunt down important incident metrics across different files or systems. How often are injuries, illnesses, near-misses, and uncontrolled hazards encountered by workers performing the job? What is the outcome and impact of those incidents? The answers to questions like these are important considerations when evaluating risk, and making this information easier to access and understand increases the likelihood that they will be incorporated into JSA risk assessments.
VelocityEHS Can Help!
Paper and spreadsheet-based systems simply lack the flexibility and shareability EHS professionals need to use JSAs to their full potential. VelocityEHS JSA software gives you the tools to overcome these limitations while providing a standardized, intuitive interface for conducting JSAs step-by-step (including job task breakdown, hazard identification, risk assessment, control implementation, and JSA reviews) so your JSA teams can do them the same way, the right way, every time.
VelocityEHS JSA software capabilities also enable you to quickly and easily select standard controls for identified risks from a drop-down menu, apply industry-standard risk reduction factors, and then automatically calculate risk reductions based on the selected controls, helping to significantly reduce potential for errors in risk assessment and control selection.
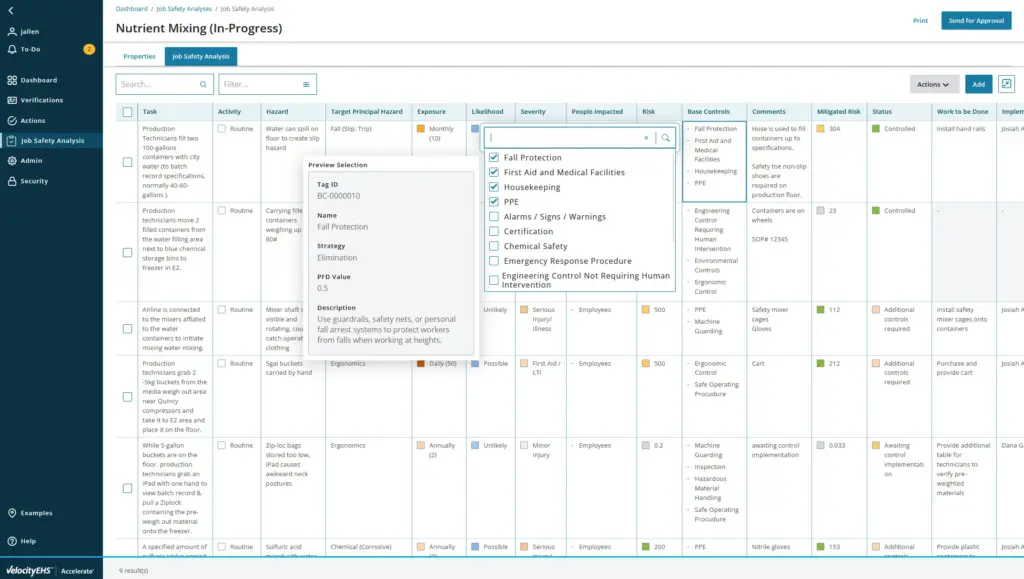
In addition, VelocityEHS Incident Management software provides comprehensive injury and illness recordkeeping capabilities including powerful reporting and data dashboard tools that allow you to quickly access and reference the incident data you need to help you refine your JSA risk assessments. With a more accurate, standardized, and informed view of job task risks in your workplace, you’ll be able to put the right controls in place to protect your workers and manage risks to the greatest extent possible. From there, you can also utilize our Audits and Inspections software to schedule, assign, and perform regular follow-ups to verify that controls prescribed in the JSA are in place and performing as expected.
Click here to request a demo today and see first-hand how VelocityEHS JSA software can help you give your JSAs a serious upgrade.