by Phil Molé
VelocityEHS recently presented the webinar “Major Chemical Safety Incidents- A Review of Common Causes” with EHS Today. The webinar reviewed investigations of major chemical incidents by the Chemical Safety Board (CSB), looking into the details of each for takeaways about common failings of risk management, and how we can address them.
In what follows, we’ll see what insights we can gain from poll questions posed during the webinar, and some of the questions and comments received from attendees.
Poll Results on Root Causes of Major Chemical Accidents
The first poll question we asked attendees early in the webinar was: “Which of the following root cause categories do you think is most common in the CSB incident investigations we will be looking at today (Choose up to three)?” The choices for the poll were:
- Hazard Analysis/PHA
- Control of Work
- Personal Protective Equipment (PPE)
- Regulatory Oversight
- Management of Change
- Safety Culture
- Recommendations/Lessons Learned
- Emergency Response
- Training/Competency
- Mechanical Integrity
- Human Factors
We intended for this question to provoke some thought among audience members about the root causes they thought would be most common, and then compare that to the actual root causes that most CSB investigations identified as being the most common according to our statistical analysis of reports. A summary of the results are shown in the chart below.
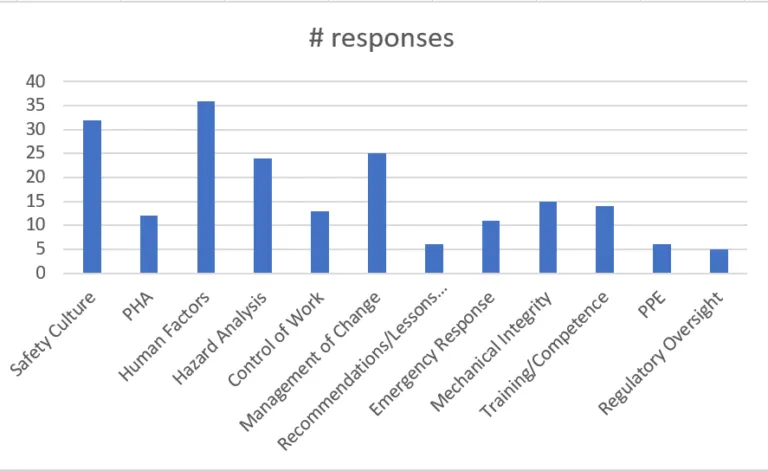
These results show that attendees thought that the top three root causes of major chemical accidents were management of change (25), safety culture (32), and human factors (36). How did these picks stack up against the results our statistical analysis from CSB investigations? Let’s find out by looking at the table below.
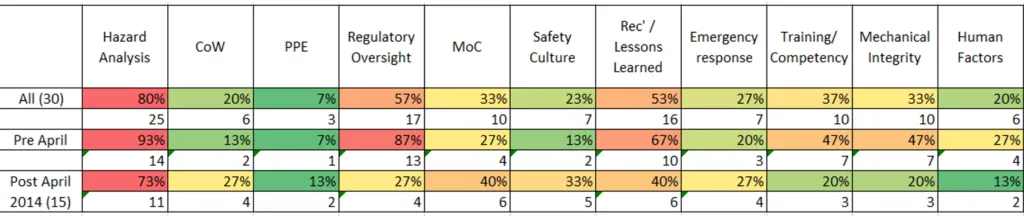
Our analysis of the CSB investigation reports reveals the three most common root causes to be “hazard analysis,” “regulatory oversight,” and “recommendations/lessons learned.” The fact that “hazard analysis” was a root cause in 80% of incident investigations shows that at a very fundamental level, most accidents result from the facility management not identifying and controlling all risks.
Poll Results on Risk Management Tools Currently Used by Attendees
The second poll question we asked, near the end of the webinar, was: “What tools are you currently using to manage risk (Choose all that apply)?” The choices offered were:
- Paper spreadsheets
- Desktop applications (Excel spreadsheets, etc.)
- Legacy on-site software systems
- Cloud-based software
- Other
The results from attendees are summarized in the chart below.
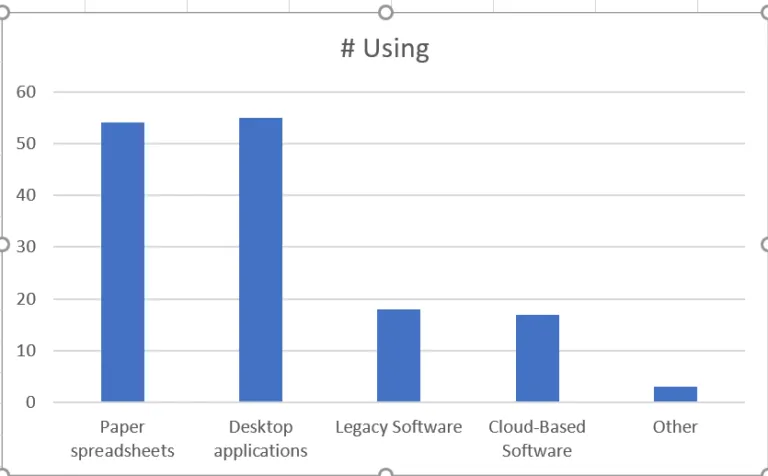
We can see from this chart that paper spreadsheets and desktop applications were by far the most common risk management tools among poll respondents. This is not that surprising, in our experience, given that many of EHS professionals who contact us report using desktop applications and hard copy spreadsheets. But it may be related to the trends we discussed above, related to common root causes identified through our review of CSB investigations.
For example, hard copies and desktop applications make it more difficult to complete hazard studies and other risk assessments, and especially difficult to share accurate knowledge of risk pathways with your workers. Cloud-based software can make it easier to assess risks, communicate a common understanding of risk to your workers, and ensure that the right controls are in place.
Key Takeaways
One interesting difference between the anticipated and the actual identified root causes is in the weighting of “human factors.” Webinar attendees thought that human factors would be the most commonly identified root cause, but our statistical analysis shows that the CSB identified “human factors” as a root cause the least often.
What might we learn from this? Human factors are a broad category that means different things to different people, and it can sometimes also encompass some structural or safety management system components, but it mostly refers to gaps in awareness or lapses of judgement in individual employees. Trained investigators like those at CSB are most likely more focused on the structural rather than individual issues, because so much research and industry knowledge shows that this is where we should be looking. OSHA, for example, defines “root cause analysis” as “fundamental, underlying, system-related reason why an incident occurred that identifies one or more correctable system failures.”
Note the repeated use of the word “system” within that definition. While it may be comforting or seem like common sense to attribute accidents to mistakes made by individual workers, underlying those mistakes are systemic issues that made the mistakes more likely.
Some of the attendees touched on this through their live questions, asking whether management or employees were ultimately responsible for safety. While of course both have their roles, we should remember that it falls on management’s shoulders to properly equip the workers with everything (knowledge and assets) they need to perform their jobs safely. This includes relevant hazard analysis, proper training and communication of hazards, and the controls to mitigate risk.
We might then ask, as some attendees did, what competencies plant management most needs in order to prevent incidents. Risk and Process Safety Management expertise would definitely help at the management level to identify these issues before they become threats. A lack of safety culture can lead to underuse of lessons learned, and increases the chances of failing to follow best practices. Some management just haven’t experienced the wrong side of bad PSM systems yet. A quote from the late chemical engineering safety advocate Trevor Kletz puts it best: “If you think safety is expensive, try an accident!”
Knowing how to do hazard analysis properly is also an important competency, because our review of the CSB data shows that inadequate hazard analysis was a root cause in 80% of the CSB incidents analyzed. Hazard analysis is fundamental to preventing accidents in ways that other safety management tools, while valuable in their own right, cannot replicate. For example, drills can be useful to ingrain emergency response situational thinking into workers. However, there are so many variables when a major accident occurs that it is hard to account for all scenarios in drill exercises. Good hazard analysis, on the other hand, is more likely to help us identify and control these risks.
All of this reinforces the importance of a safety management systems approach to risk, focused on ways of making it easy to do the right thing. Modern cloud-based software like Risk Management from VelocityEHS can give you the tools to easily map your risks using bowtie analysis, keep all of your workers well-informed about risks, and verify that controls within your risk pathways are installed and properly working.
Additional Resources
The poll information shared in this blog is only one small part of the webinar on chemical accidents, which is now available on-demand in the link below.
Major Chemical Safety Incidents – A Review of Common Causes
Looking for more information about how to improve your risk management? You can download our risk bowties infographic to learn why risk bowties can help you develop and share an accurate view of risk pathways with your workers:
Risk Bowties: A Tool for Risk Management and Training
And if you’d like a really deep dive into risk management, register for our upcoming 8-hour, 2-day training course:
Introduction to Bowtie Analysis: An 8-Hour Virtual Training Course
We’re always adding more content to our blog and our Resources page, so be sure to check back often!
Let VelocityEHS Help
Our customers consistently report that our bowtie analysis capabilities have helped them achieve dramatic improvements to workplace productivity, knowledge sharing and risk management program performance.
Bowtie analysis is just one of many tools within our Risk Management solution, which also includes risk registers, qualitative and quantitative risk analysis, layers of protection analysis (LOPA), critical controls verification and much more!
Ready to see more? Visit our Risk Management page to request a demo with one of our customer solutions consultants today!