Standardize your JSA Process with Job Safety Analysis Software
Create a standardized JSA process that works for your organization. Ensure data accuracy and easily identify and calculate risk to prevent injuries and illnesses for workers. Great news: JSAs are available on the Accelerate Platform.
Standardize JSAs with configurable templates
Improve accuracy & auto-calculate risk scoring
Gain real-time visibility into JSAs with custom dashboards
Job Safety Analysis software helps you efficiently manage the entire JSA process across locations – to accurately identify hazards to your workers, easily verify controls and prevent dangerous and costly incidents from occurring. Available on the on the VelocityEHS Accelerate® Platform.
JSA Core Capabilities
Configurable JSA Template
Base Control Library
Standardized Worksheets
Hazard and Control Trending
Risk Reduction Action Items
Auto Risk Calculation
Configurable JSA Template
Base Control Library
Standardized Worksheets
Hazard and Control Trending
Risk Reduction Action Items
Auto Risk Calculation
Video
Getting More from Your JSA Process
The new Job Safety Analysis (JSA) capability in VelocityEHS Operational Risk is designed to standardize JSA across your locations, simplifying and streamlining this essential safety and risk management process to help you get more from much less effort.
Watch the quick video to learn more.
Benefits of VelocityEHS
Job Safety Analysis (JSA) Software
Standardized JSA
Processes
- Reduce data variability with JSA templates configured to your organization’s process
- Determine severity, likelihood, number of people involved and exposure of identified hazards
- Create a library of base controls with associated risk reduction factors
- Assign actions & automate notifications for deadlines.
Improved Data Accuracy & Utilization
- Reduce data entry errors, create consistency, improve efficiency
- Identify trends in hazards and controls across all tasks and locations
- Auto-calculate risk score from entered hazards and risk reduction factors
- Get better insight into risk control strategy
Greater Visibility &
Engagement
- Get real-time visibility into the status of ongoing JSAs, hazard assessments and action items
- Customize dashboards to display specific safety metrics
- Boost collaboration with unlimited users & worksheets
Infographic
JSA Software Helps Solve the Puzzle of Risk
Download now to see how to make this risk analysis process simpler, faster & more valuable for your organization.
The EHS Software Revolution Has Begun
Introducing the VelocityEHS
Accelerate® Platform
The industry’s first truly integrated EHS platform on the market, streamlining Velocity’s Safety, Ergonomics, Chemical Management, and Operational Risk capabilities into one seamless solution.
Activations are underway. Secure your spot today!
Prevent Harm
Send workers home safe with solutions that cover a range of risks.
Drive Engagement
Reduce training time and simplify complex tasks with in-app guides.
Save Time
Free managers from tedious administration with centralized controls.
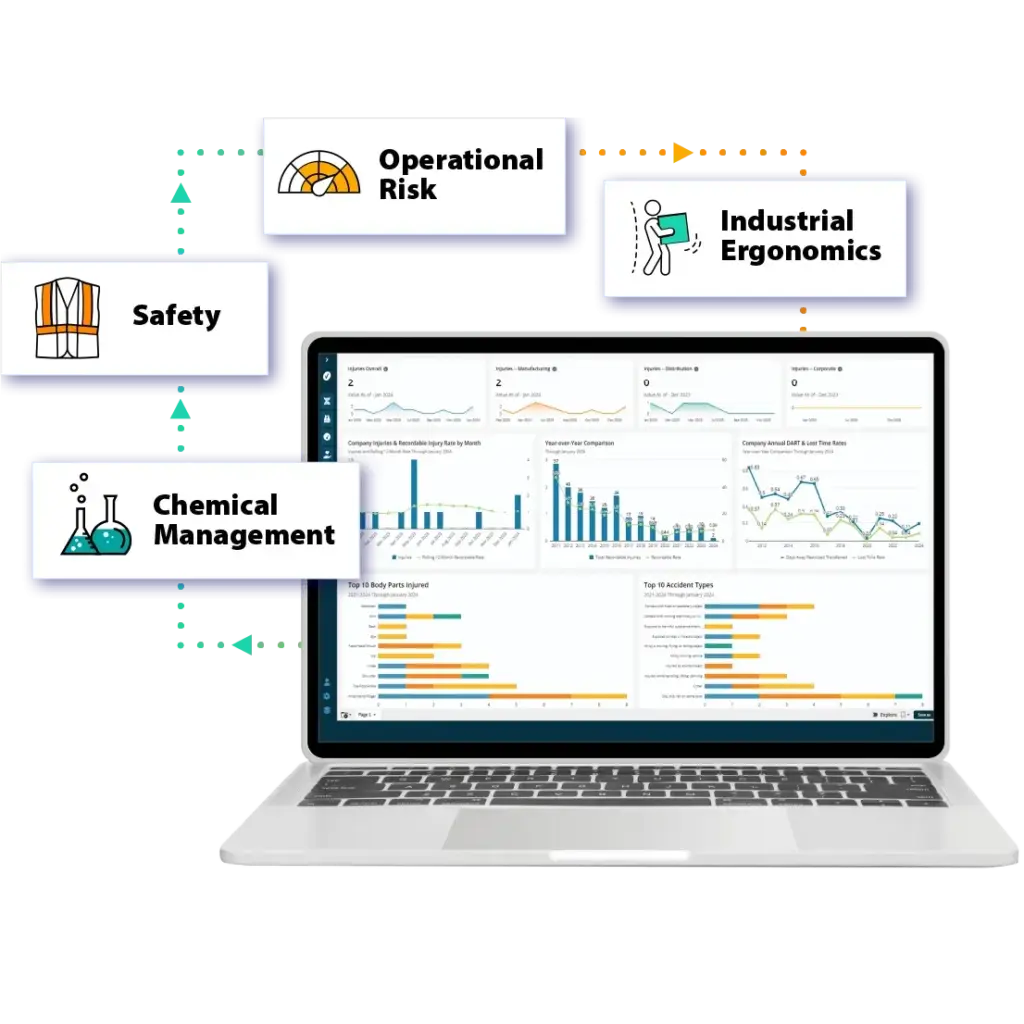
Be Predictive
Anticipate & address risk with real-time data you can trust.
Increase Visibility
Unite every level of your organization via shared dashboards & reports.
Embrace Innovation
Harness machine learning + AI & automation to deliver expert-level results, faster.
How can VelocityEHS help you with your JSAs?
The VelocityEHS Operational Risk Solution makes the JSA /JHA process faster, simpler and smarter.
Ditch paper and spreadsheets for a centralized software system that helps your team members easily document hazards and select controls, track corrective actions, and share results with other people — instantly. Standardized digital JSAs means more accurate, usable data to help your organization prioritize its safety and risk management efforts. Easy access to hazard information and preventive measures means a safer and more efficient workplace for everyone.
Job Safety Analysis (JSA) FAQ
Helpful Resources
What’s New in Operational Risk?
Check out the latest operational risk industry news, our latest blogs, and helpful training resources to ensure you stay ahead of the curve.
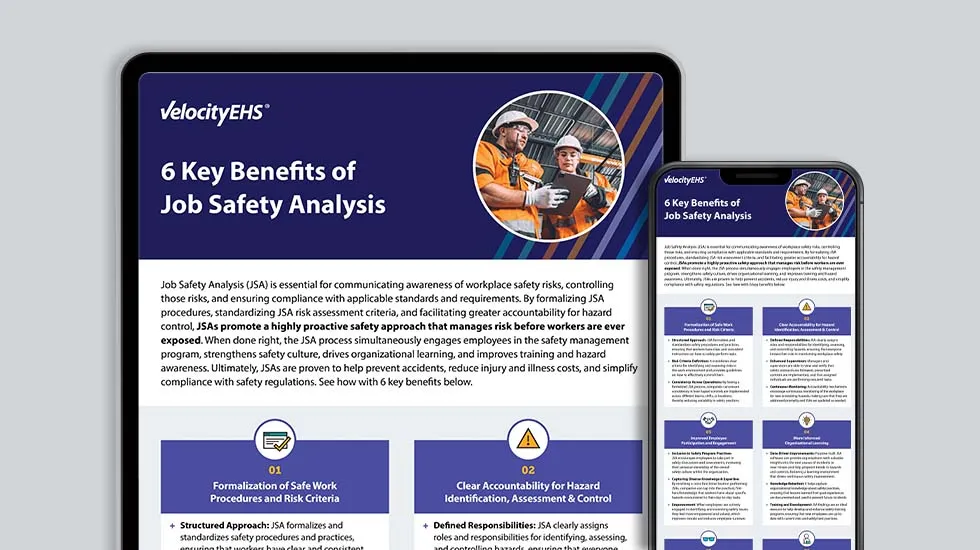
6 Key Benefits of Job Safety Analysis (JSA)
Guide
Operational Risk
Download this guide now to learn why JSA is essential to improving safety and reducing risk in your workplace.
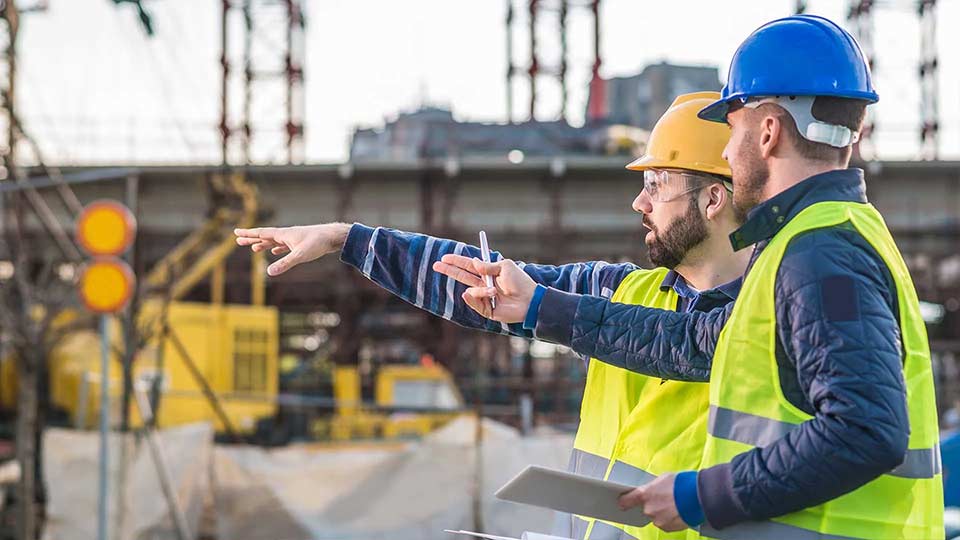
Are Your JSAs Good Enough? Don’t Wait for a Workplace Incident to Find Out
On Demand Webinar
Operational Risk
Don’t wait until an incident happens before you investigate how well your JSAs are working. Learn the 5 key characteristics for effective JSAs.
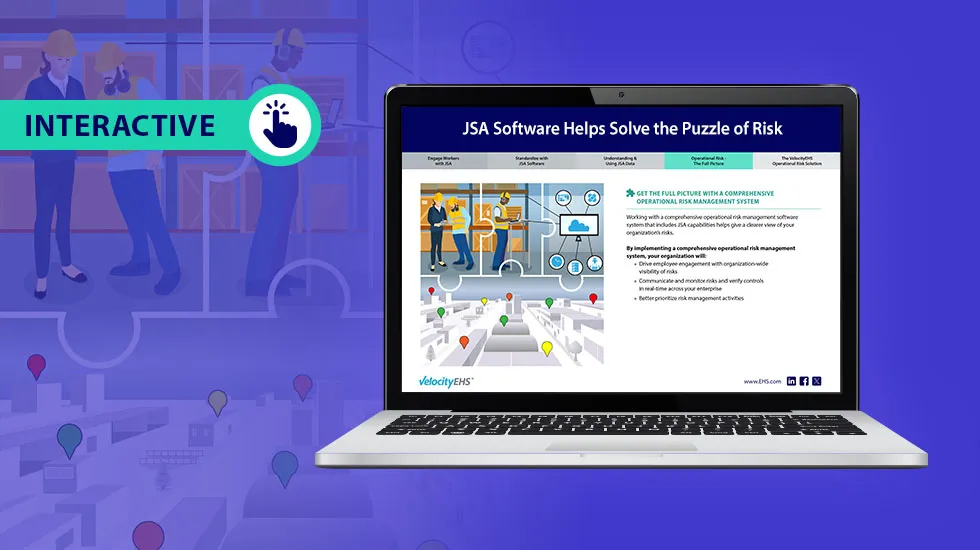
JSA Software Helps Solve the Puzzle of Risk
Infographic
Operational Risk
Download this infographic to see how to make Job Safety Analysis more effective for your organization.
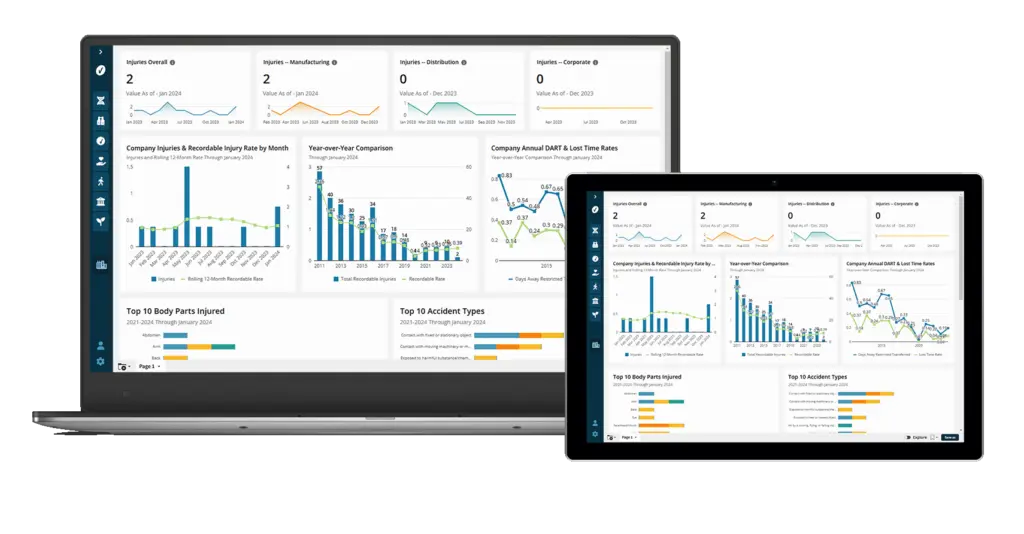
Schedule a Demo Today
You’re not just buying software or services—you’re investing in a partnership that empowers your team to proactively solve problems and move boldly into the future.